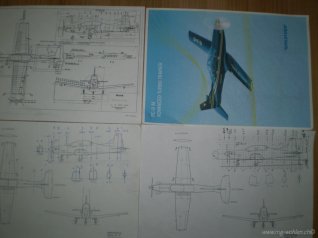
Unterlagen der PC-9 aus dem Internet
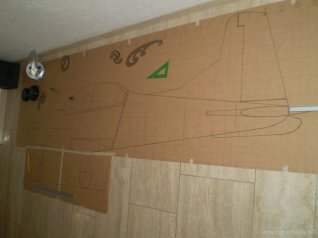
Seitenansicht auf 3 Meter Packpapier
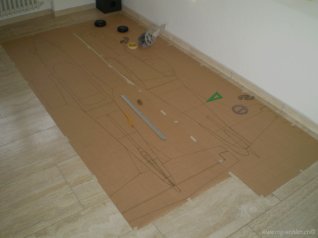
Jetzt mit der Draufsicht

Positionen der Rumpfspante sind festgelegt
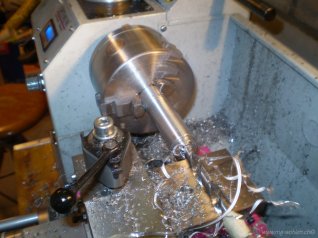
Herstellung von ersten Fahrwerkteilen
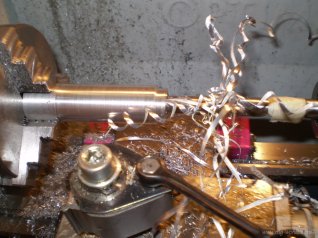
Viele Späne!
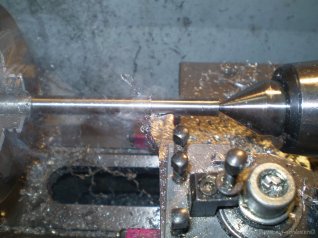
Die Stossdämpferteile sind aus Titan (Danke Koni!)
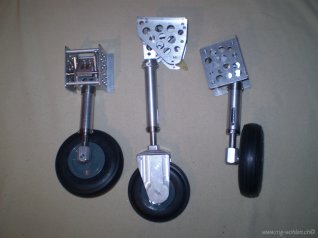
Alle 3 Fahrwerke endlich fertig
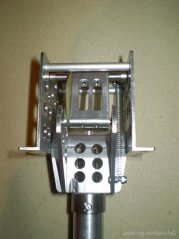
Mechanische Verriegelung über Totpunkte in den Ein-Aus Positionen, hier das Bug-FW in Position aus
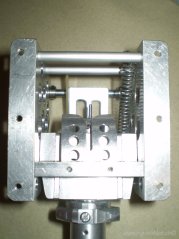
Kulisse der Radzentrierung des BFW in der Aus-Position, somit steuerbar
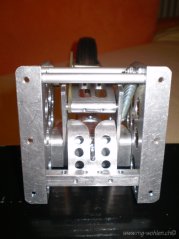
Hier in der eingefahrenen Position ist das Rad zentriert
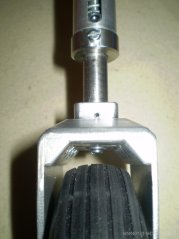
Bugfahrwerkgabel aus 3 Frästeilen
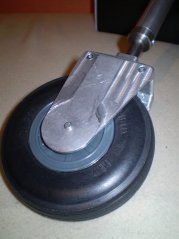
Bugfahrwerkgabel von der Seite
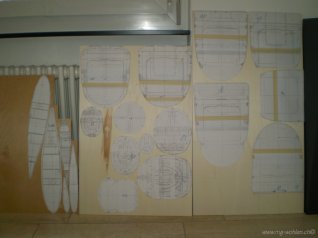
Rumpfspante und Musterrippen auf Sperrholz geklebt
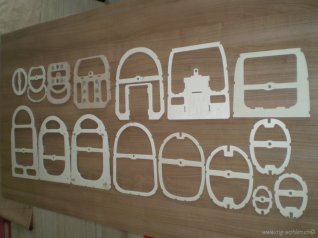
Alle Rumpfspante (nix CAD!) aus 4 mm Pappel-SpH, Motor- und Bugradspant aus 8 mm Flzg.-SpH herausgedremelt
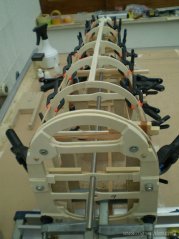
Heckkonus-Rumpfspante sind mit 3x8 mm Kieferstringern verbunden
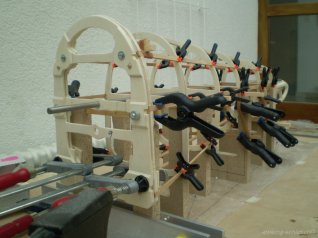
Die Spante sind auf einem 8 mm Rundstahl aufgefädelt und ausgerichtet
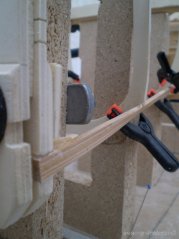
Mit Wässern werden die Spanten spannungsfrei gemacht
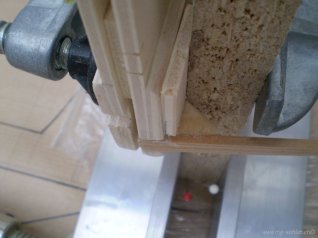
Zur Sicherheit werden bei der Rumpftrennstelle Eckstücke verleimt
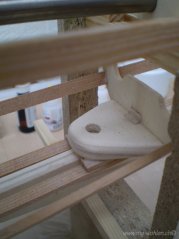
Untere Lagerung des 8 mm Kohlenrohr-Seitenflossen-Holmes
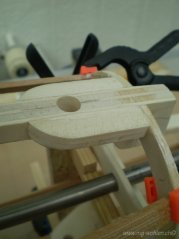
Obere Lagerung des Kohlen-Holmes
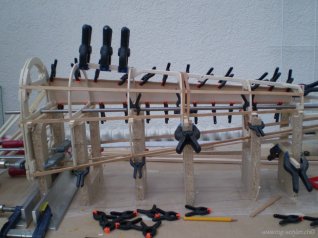
Die erste Beplankung vom Heckkonus wird verleimt
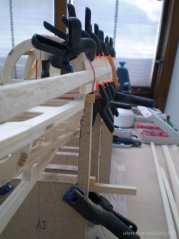
Grossflächige Pressungen ergeben später weniger Schleifarbeit
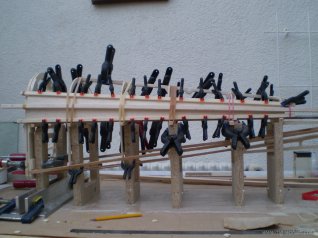
Die 2. Beplankung verleimt
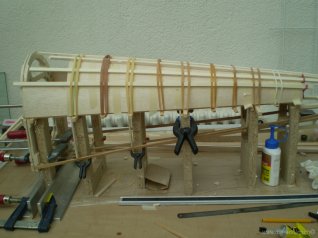
3. und 4. Beplankung
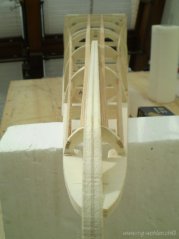
Unterseite vom Heckkonus
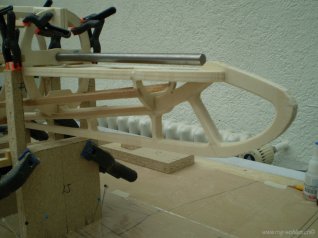
Kern der unteren Rumpffinne (10 mm Pappel-SpH) massiv erleichtert
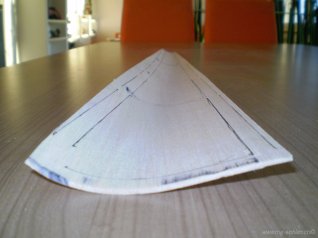
Die 3-dimensional gebogene Rumpfbeplankung mittels Wässern der Rumpfform angepasst
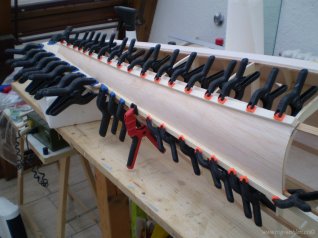
Die gewässerten Rumpfbeplankungen werden verleimt (Rumpfunterseite)
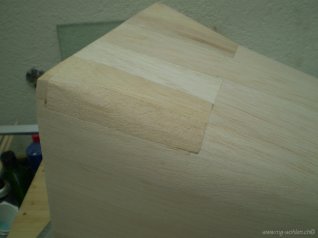
Ohne Füllklötze (unten) gehts aber doch nicht
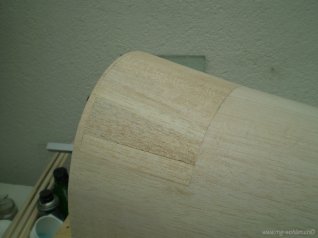
Die oberen Füllklötze schon mal grob verschliffen (Übergang zum Capot muss später noch angepasst werden)
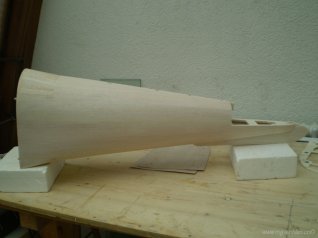
Das ganze 99 cm lange Stück wiegt jetzt nur 658 Gramm!
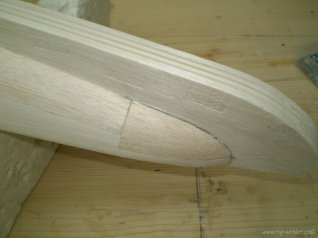
Die hintersten Füllklötze
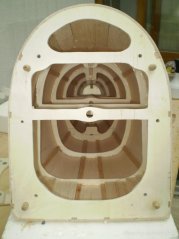
Klassische Holzbauweise (Die Führungsstege werden später noch weggeschliffen)
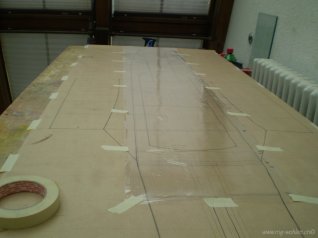
Vorbereitungen für den Rumpfvorderteil
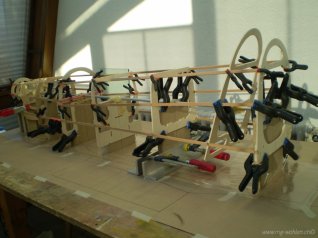
Spanten mit Stringern (auch 3x8 mm Kieferleisten) verbinden wie gehabt
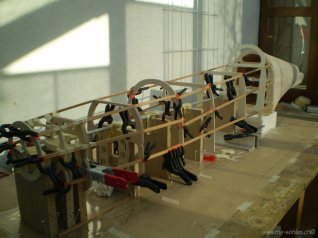
Kontrolle der Ausrichtung des Hinter- mit dem Vorderteiles mit den 8 mm Rundstählen
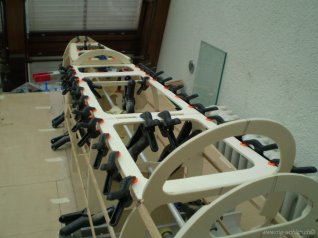
Verstärkungen im Bereich von der Haube und für Motor-Batterien-Deckel
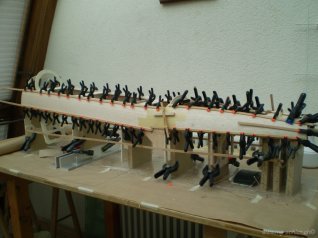
Beplankungen Nr. 1, 2, 3 und 4 des Rumpfvorderteiles
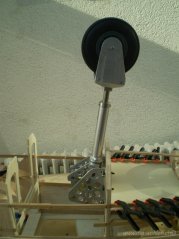
Das Bugrad wird eingepasst
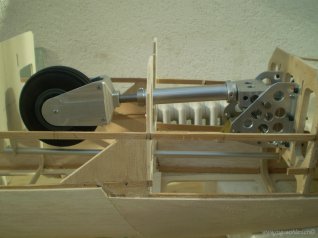
Das Bugrad fährt im Gegensatz zum Original voll in den Schacht ein (wegen des Kühlluftaustrittes)
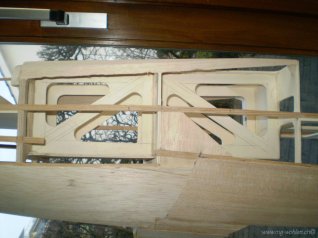
Die Bugradschacht-Seitenwände werden erst später mit 1 mm Balsa beplankt
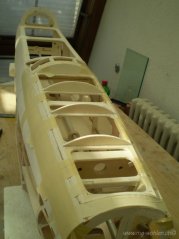
Die Beplankungen Nr. 5 und 6 sind verleimt
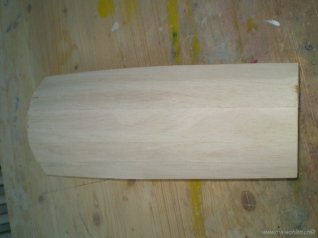
Der Deckel für den Motor-Batterieraum
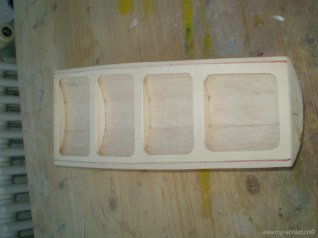
Unterseite des Deckels
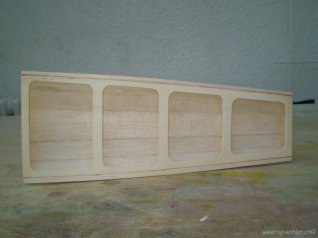
Dieses 45 cm lange Ding wiegt vor dem Verschleifen ganze 83 Gramm
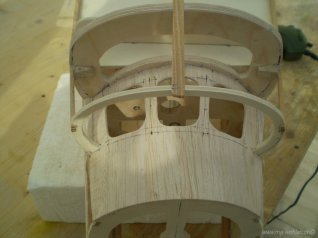
Die 3 Aussparungen sind für die Motorkühlung
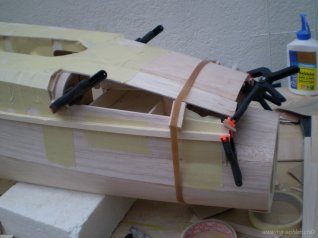
Weiter gehts mit der 3 mm Beplankung
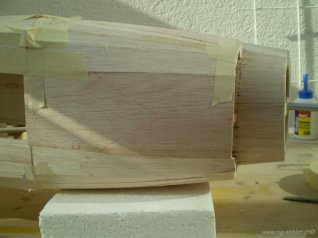
Die letzten Rumpfbeplankungen sind verleimt
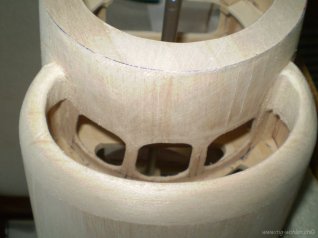
Schon mal das Näslein grob verputzt
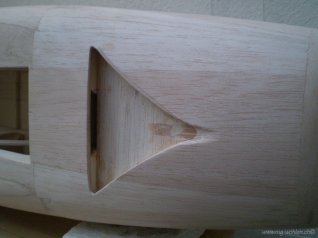
NACA-Einlass für die Reglerkühlung
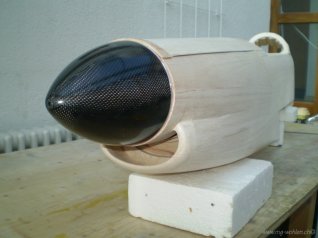
Das wird noch gewaltig Balsastaub geben!
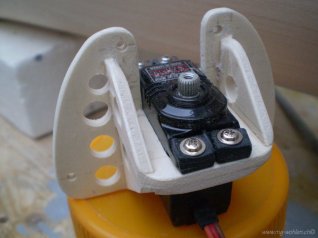
Der Träger für das Seitenruder-Servo
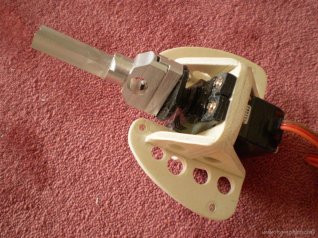
Wirklich eine direkte Seitenruder-Ansteuerung
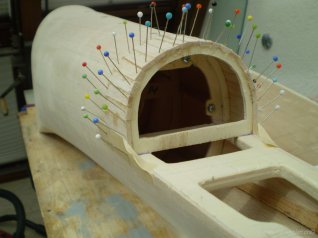
Die Abdeckung für das Seitenruder-Servo wird aufgebaut
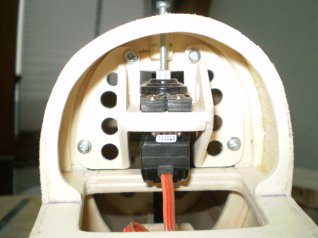
SR-Servo eingepasst und zentriert
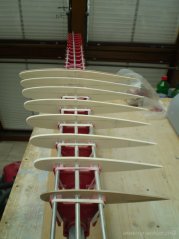
Höhensteuer-Musterrippen aus Pappel-SpH (alle Musterrippen werden an den Kanten mit dünnflüssigen CA-Kleber gehärtet)
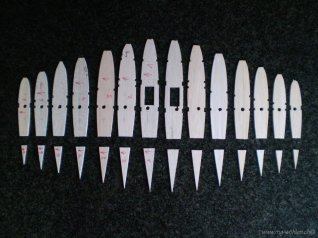
Einbaubereite Höhensteuerrippen
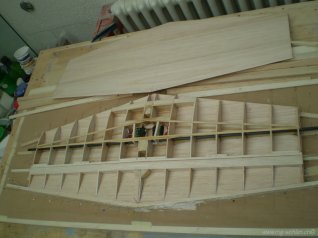
Höhensteuer ist auf der oberen Beplankung (durchgehend gerade Endkante) aufgebaut und verleimt
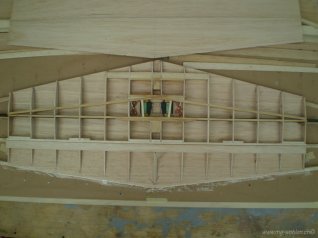
Zwischen Flossen- und Ruderholm sind 1 mm Balsastücke für den späteren Ruderspalt
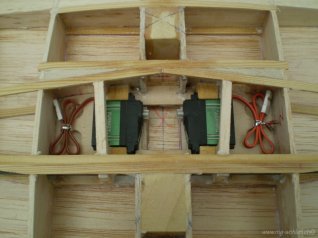
Beide HR-Servos sind eingepasst
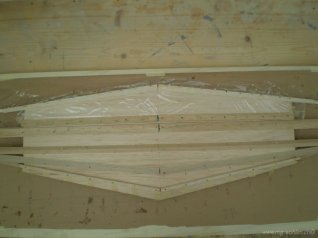
Auch die untere Beplankung wird an einem Stück aufgebracht

Habe den 1 mm Spalt zwischen den beiden Holmen sogar getroffen!
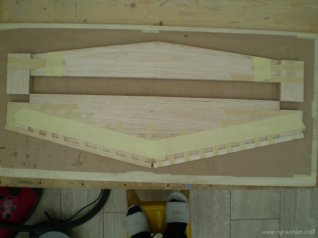
Nasenleisten und Randbogen sind mit verdicktem Epoxy verleimt

Grob verschliffen und am Rumpf angepasst
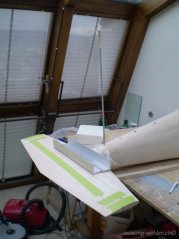
Auch der Winkel zum Seitenflossenholm stimmt, nun werden die Bohrungen für die Befestigungsschrauben auf den Rumpf übertragen