
Aufbau des Haubenrahmens

Gerüst des Haubenrahmens

Vorbereiten für das Vacuum-Ziehen der Haube bei der Firma Grütter Kunststoffe in Hombrechtikon

Bohrungen für die Befestigung des Positives auf der Alu-Grundplatte mit den Vacuum-Kanälen

Gleich machts pffft!

Sieht schon mal nicht schlecht aus

Entformen nach dem Pffft

Das dritte Stück aus 1.5 mm Polycarbonat kann verwendet werden, diejenigen aus 1 mm -Material waren an den Rändern zu dünn

Grobes Anpassem am Rohrahmen

Alle Anschrägungen des Rahmens an der Haube sind angepasst

Belegung und Pressen der Kohlebänder als Versteifungen des Rahmens

Jetzt ist der Capot-Rahmen knüppelsteif!

Der ganze 70 cm lange Rahmen wiegt jetzt nur 118 Gramm!

Der Rahmen ist am Rumpf endgültig angepasst

Feder der Hauben-Verriegelung

4fach-Verriegelung der Haube

Hier die vorderste Verriegelung

Die ganze Verriegelungsschiene mit dem äusseren Handgriff

Dreh- und Verriegelungspunkte (je 4 Stück) des Capots

Der Haubengriff aussen
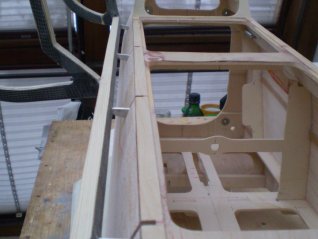
Das Capot ist leichtgängig angeschlagen

Die Drehpunkte an der rechten Aussenseite

Der Hauben-Offenhalter bei offener Haube

Kompletter Offenhalter mit Beschlägen aus einem Kohlerohr und Fräs-Drehteilen aus Alu
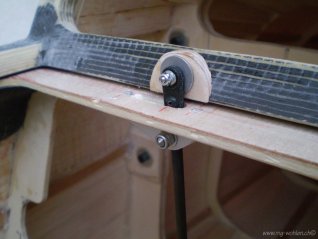
Eingefahrener Halter bei geschlossenem Capot
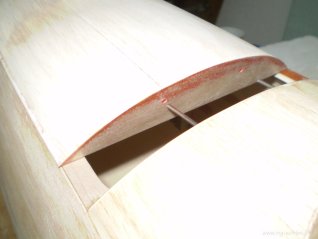
Doppel-Verriegelung des Deckels für den Motor-Batterieraum

Deckel-Verriegelung kabinenseitig

Bei geschlossenem Capot ist die Deckelverriegelung gesichert

Endgültiges Anpassen der Haube auf den Rahmen

Verleimen von Haube und Rahmen mit verdicktem (Baumwollflocken) Epoxyharz

Nach dem Imprägnieren mit Holzhartgrund werden Rumpf, Flügel und Leitwerk mit 25 gr-Gewebe geglast

Hauptfahrwerktore und Radhutzen werden am Mittelflügel angepasst

Die inneren Fahrwerktore von den Hutzen sind an der richtigen Stelle herausgetrennt

Die Tore werden jetzt angepasst

Die nur 0.6 mm dicken Hutzen werden mit Balsastegen versteift

Alle Aufhängungen für die 6 Fahrwerktore

Bugfahrwerktor-Aufhängungen demontierbar eingebaut

Balsastege in allen Fahrwerktoren, sie werden mit einem Kohlengewebe überzogen, dadurch werden die Dinger bocksteif

Endgültiges Anpassen der anscharnierten und demontierbaren Fahrwerktore

Auch alle Anlenkbeschläge an den Toren sind jetzt montiert

Die inneren Tore werden sequenziert angesteuert und sind nur beim Aus-Einfahren der Hauptfahrwerke offen

Innere Hauptfahrwertore mit den mit Kohlengewebe überzogenen Balsastegen und dem Anlenkwinkel

Bugfahrwerktore geschlossen mit grosser Kühlluftaustrittsöffnung dahinter (beim Original schaut hier das Bugrad zu ca. einem Drittel raus)

Bugfahrwerktore geöffnet

Einbau der Akku-Weiche unter der hinteren Panel-Abdeckung

Alle 6 Leuchtdioden der Weiche sind durch nur 0.8 mm grosse Bohrungen in der Abdeckung sichtbar

Rohe Einzelteile der Schleudersitze

Etwas Material für die Besatzung (für was alles man Christbaumkugeln verwenden kann!)

Die ersten Sitzproben

Das Gurtschloss ist ein Dreh-Frästeil aus Alu

Die Instrumente im Viertelmassstab sind (fast) originalgetreu aus dem Internet entstanden

Helmvisiere aus einer leergetrunkenen Rivellaflasche

Die Sauerstoffmasken sind aus Balsa

Der Sauerstoffschlauch entstand aus einer mit 1 mm Litzenkabel umwickelten Kabel-Silikonisolierung (160 Umgänge pro Schlauch!)

Die Hände und Steuerknüppelgriffe sind ebenfalls aus Balsa handgeschnitzt

Fast ready for takeoff

Mal von rechts vorne

Jetzt frontal von vorne

Nun von links vorne

Der Pilot in Comand himself, als Material für die Combis musste eine Sicherheitsweste das Leben lassen

Hier der etwas skeptische Passagier

Heb di fescht!!

Gleich gehts los!

Nur noch die Haube zu

Jetzt wird gestartet

Die nur 196 Gramm schwere Besatzung von hinten rechts

Von hinten links

Startabbruch! Das Flugi ist ja noch gar nicht fertig!!!