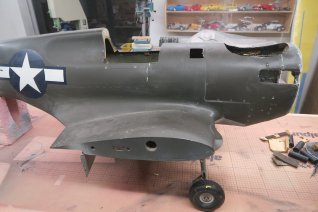
Als erstes wird das Modell begutachtet
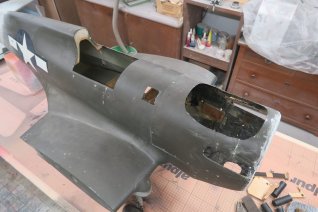
Schadstellen ausfindig machen
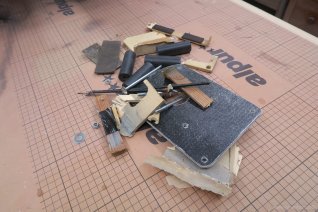
Die ersten Teile werden abmontiert
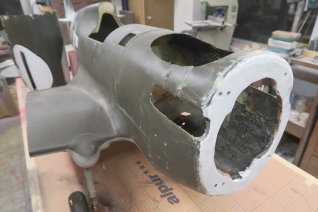
Das sieht nach sehr viel Arbeit aus
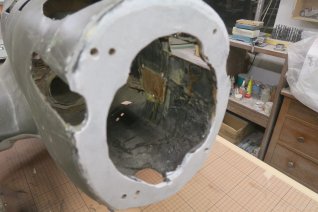
Einblick ins innere
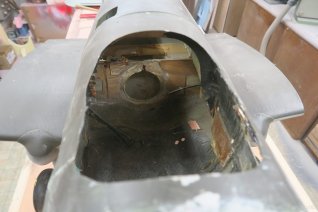
Silikon im Modellbau ist immer schlecht
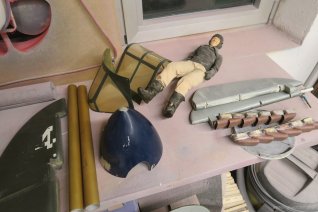
Die Frage stellt sich was noch zu gebrauchen ist
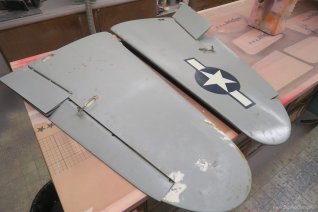
Die Flügel vom Vorgänger teilrepariert
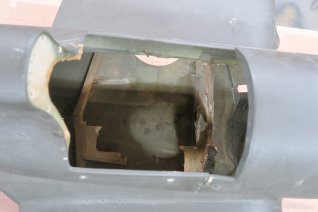
Alles was möglich ist wird herausgetrennt
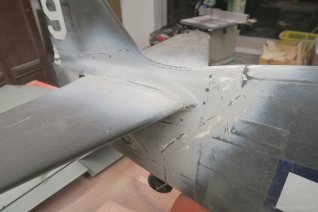
Da hat schon jemand einen Reparaturversuch gemacht
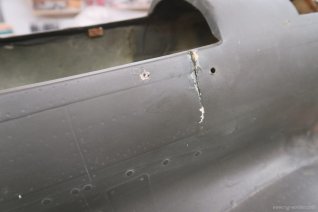
Riss in der Seitenwand
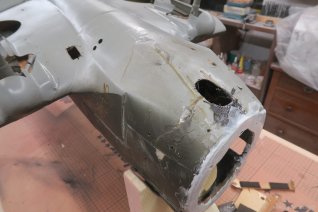
Hier darf man von Pfusch reden
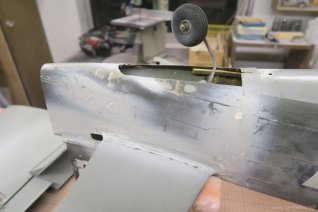
Dieses Heckrad muss raus
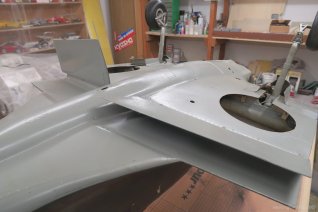
Auch die Fahrwerke werden ersetzt
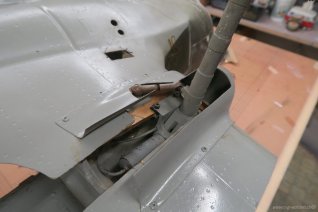
Nicht Vertrauen erweckend
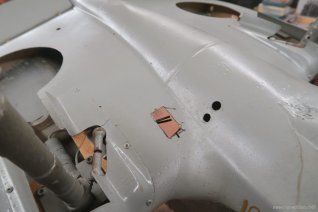
Diverse Löcher im Rumpf
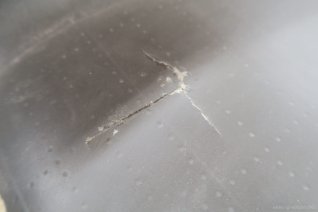
Risse auf dem Flügelansatz
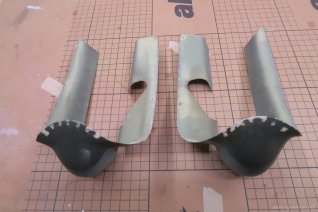
Fahrwerksverkleidung abmontiert
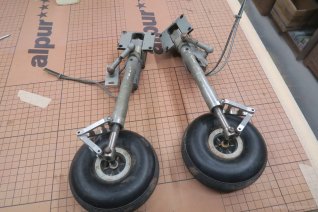
Die ausgebauten Fahrwerke
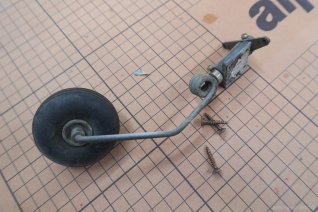
Ausgebautes Heckfahrwerk
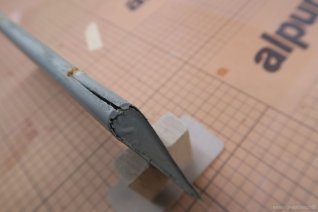
Klappenschaden
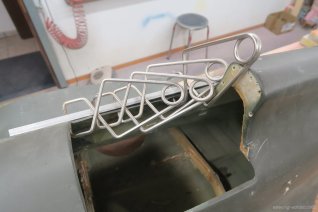
Fixiert und mit dem Heissluftföhn erwärmt
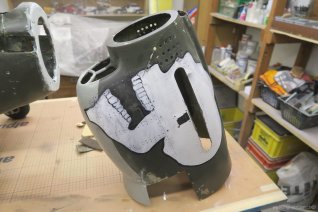
Die Haube noch einigermassen intakt
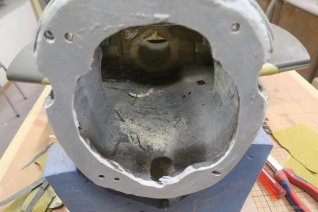
Die Innenseite grob angeschliffen
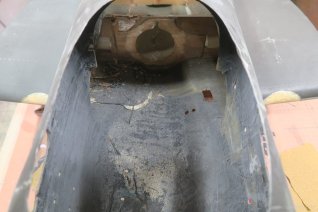
Es gibt immer mehr Platz im Innenraum
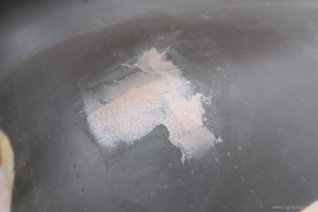
Der erste Riss im Flügel ist grob verspachtelt
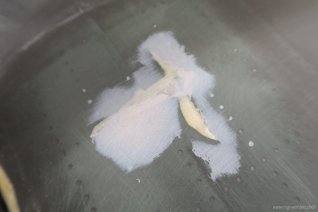
Spachtel grob verschliffen Finish kommt später
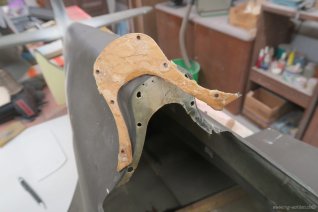
Dieser Spant war mit Wärme gut entfernbar
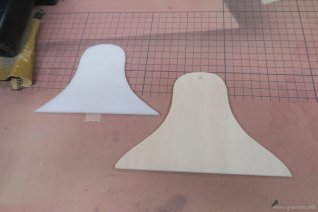
Erst ein Muster aus Depron dann ein Spant aus Pappelsperrholz
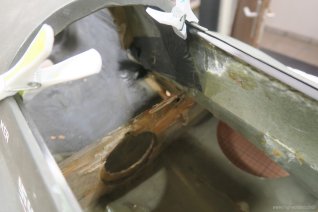
Der Haubenausschnitt wird mit CFK Rohre verstärkt
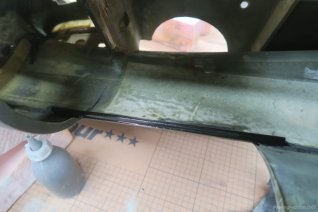
Die Rohre müssen gut verklebt werden
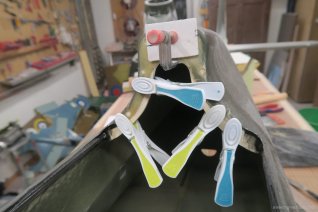
Jetzt kann der Spant eingeklebt werden
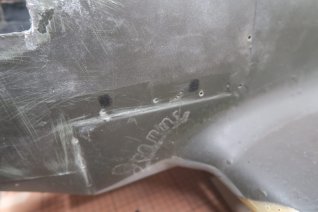
Überall sind Löcher zu verschliessen
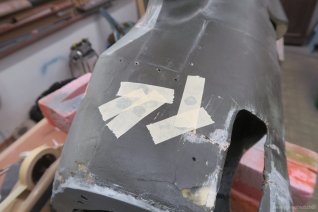
Mit Kreppband abgedeckt ergibt es eine ebene rauhe Oberfläche
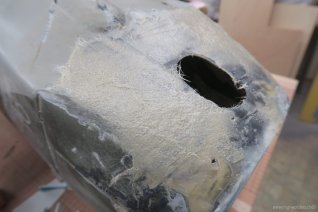
Grobe unebenheiten werden immer mit GFK verstärktem Spachtel ausgeglichen
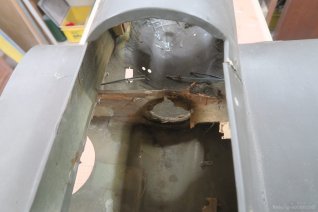
Dieser Spant muss später verstärkt werden
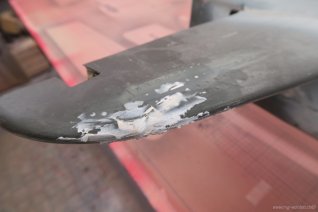
Dieser Spachtel ist noch vom Vorgänger
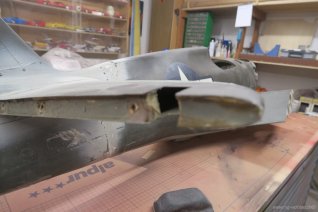
Im Höhenleitwerk fehlt ein Teil der Verkastung
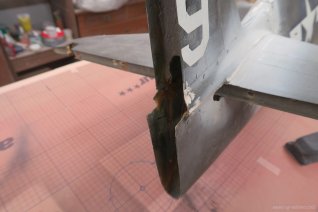
Auch hier ist Arbeit angesagt
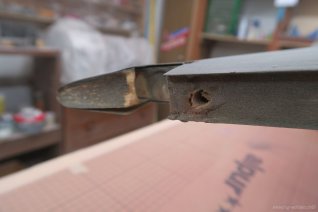
Das Laminat ist lose
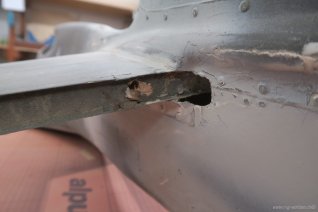
hier wurde schon mal repariert
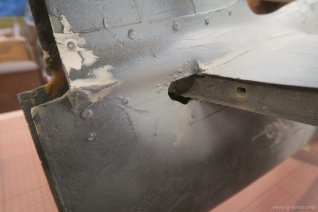
Ältere Kampfspuren
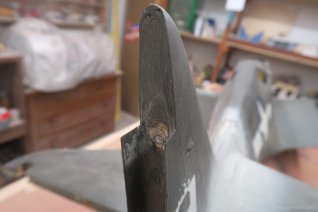
Seitenleitwerk
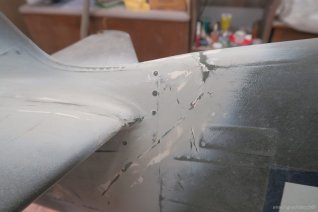
Dies muss schöner werden
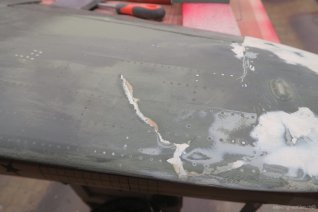
Jetzt fängt die eigentliche Reparatur an
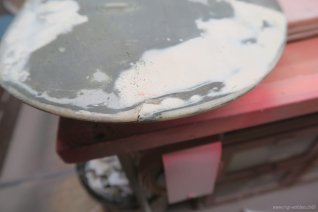
Hier wird nochmals geschliffen und aufgespachtel
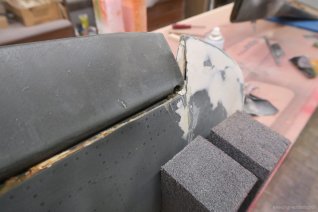
Lose Holzteile werden mit eingedicktem Harz neu verklebt
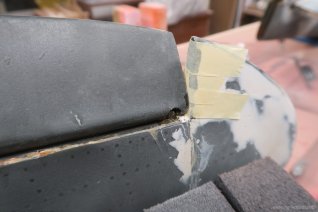
Der Harz wird mit Klebeband in die Hohlräume gedrückt und zugleich fixiert
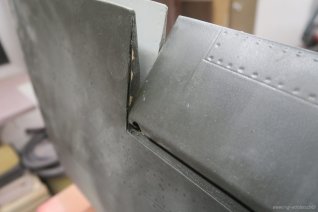
Auch hier Spalten die aufgefüllt werden müssen
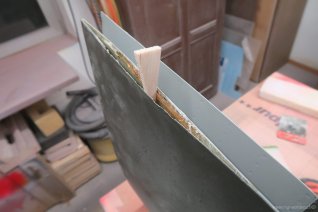
Laminat kontrollieren und neu verkleben
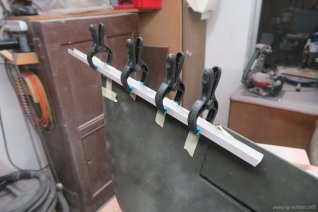
Bis zur Aushärtung schienen damit das Zeugs gerade bleibt
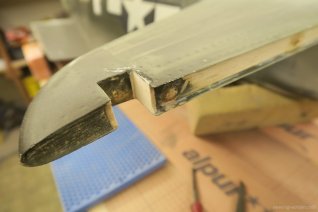
Die fehlenden Teile werden mit Balsaholz ersetzt
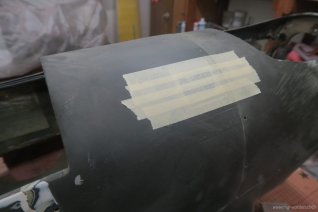
Dieses grosse Loch ist von aussen abgeklebt und von innen mit CFK verschlossen
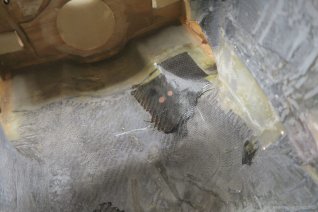
Noch mehr Löcher werden von innen zu laminiert
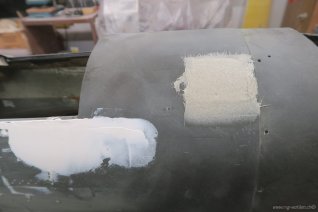
Die verschlossenen Löcher werden erstmals grob gespachtelt
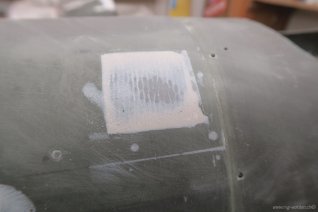
Löcher verschlossen und verschliffen
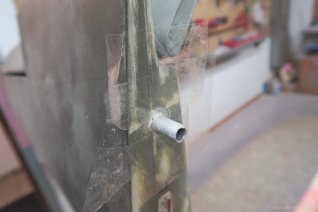
Der Flügel wird mit Klebeband abgedeckt...
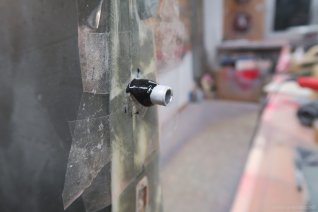
...und über den eingefetteten Bolzen eingedickter Harz aufgetragen...
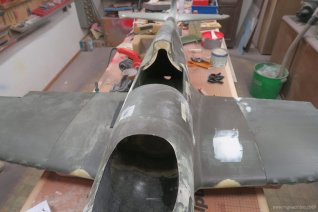
...dann wird der Flügel aufgesteckt und fixiert...
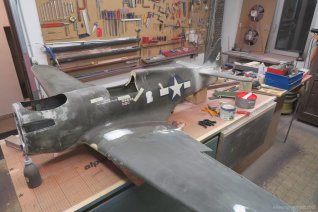
...dann passt der Flügel perfekt
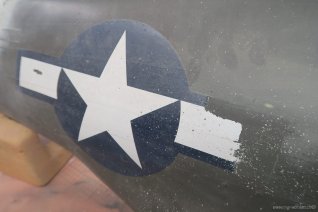
Jetzt müssen noch die Schiebebilder entfernt werden
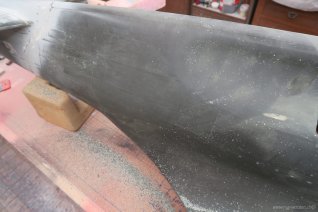
Stück für Stück der Schiebebilder wird weggekratzt
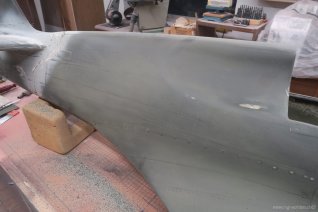
Rumpf gereinigt
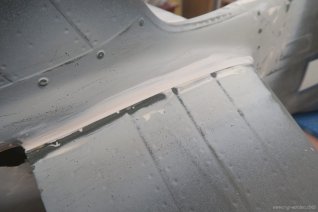
Heckflügel Anformung aufgespachtelt
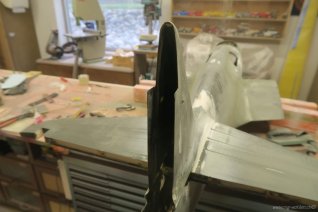
Alles wird ausgeschliffen
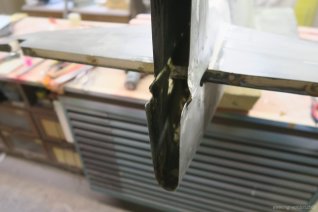
Hier wird von innen eine Verstärkung auflaminiert
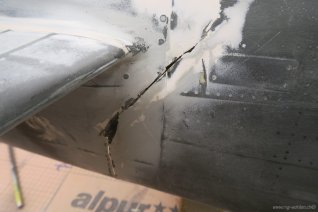
Diese Reparaturstelle hatte einen Versatz...
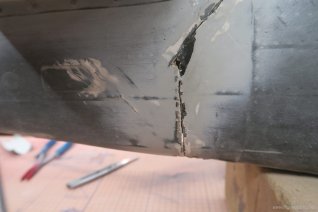
und musste aufgetrennt werden
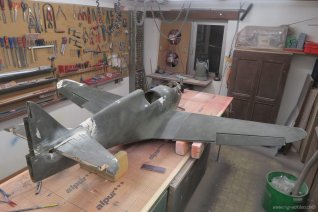
Langsam kommt Freude auf
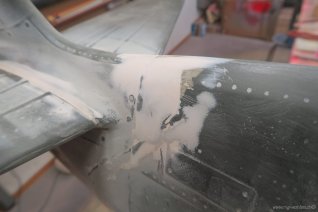
Alte Reparaturstellen neu verklebt
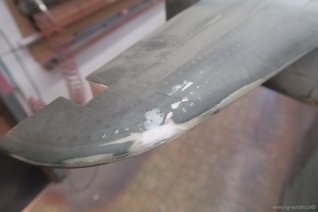
Fertig verschliffen
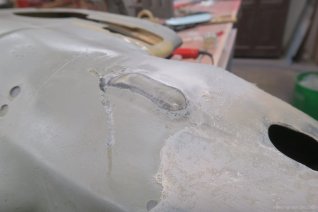
hier ist noch eine unschöne Beule unter dem Rumpf
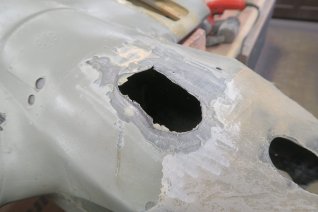
Komplette Beule weggeschliffen
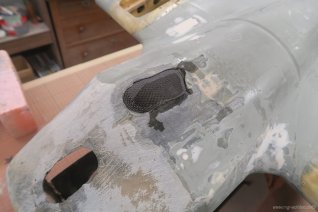
Die abgeschliffene Beule wird von innen verschlossen
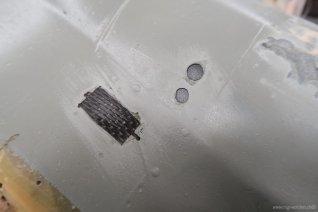
Reparaturstelle vor dem Verspachteln
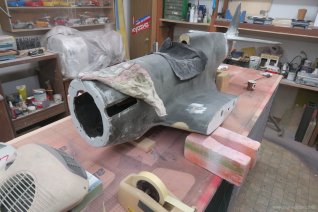
Flickstellen temperieren damit sie schneller aushärten
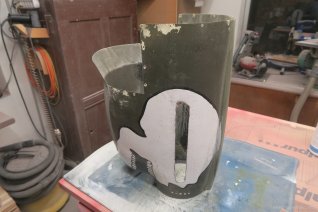
In einer Trocknungsfase kommt die Motorhaube dran
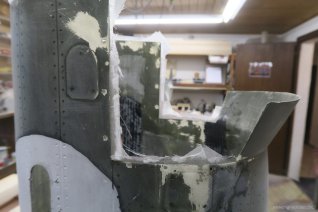
Zuerst werden die Ränder mit GFK Gewebe verstärkt
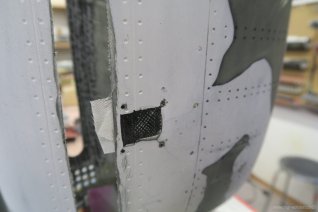
Und wieder Löcher von innen verschliessen
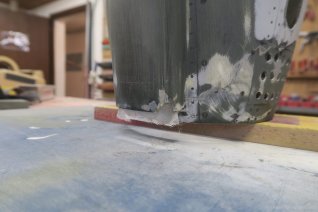
Die ausgebrochenen Stellen werden aufgefüttert
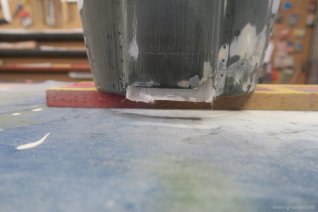
Hier muss nachher gespachtelt werden
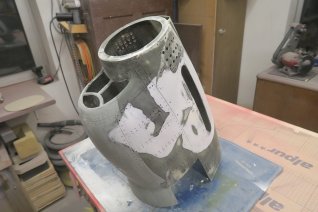
Die Haube ist jetzt rohbaufertig
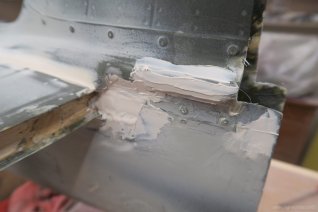
Und das Löcher verschliessen zieht sich weiter bis ins Heck
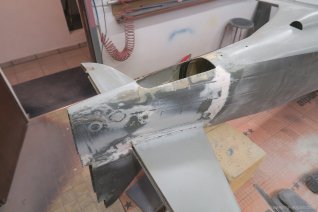
Hier sieht man die innere CFK Rissverstärkung
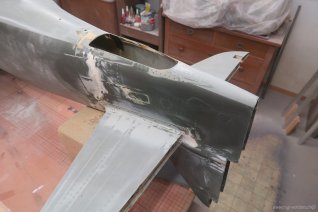
Ein grosser Teil ist schon grob verschliffen
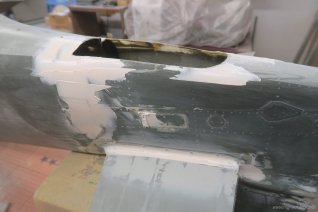
Jetzt kommt der letzte Schliff
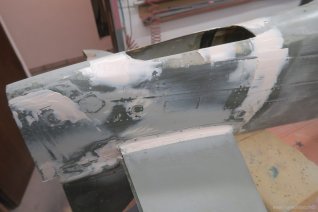
Spachtel wohin man sieht
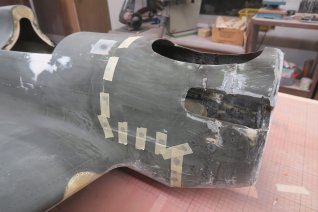
Auch die Befestigungslöcher für die Haube werden neu angesetzt
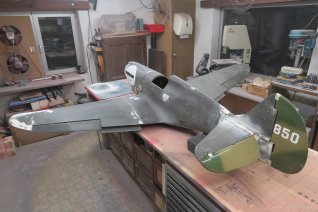
Zwischendurch mal aufräumen dann gehts weiter
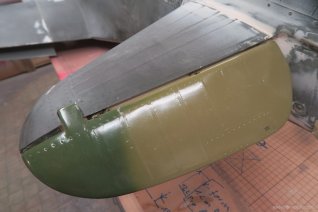
Die Scharnieren für das Höhenruder werden gesetzt
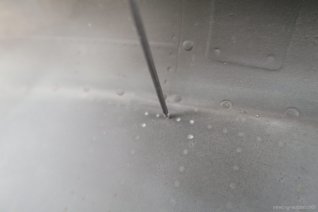
Ein Nietwerkzeug zum Nacharbeiten mit der Bohrmaschine...
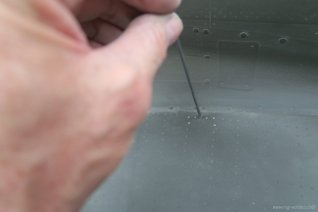
...oder von Hand...
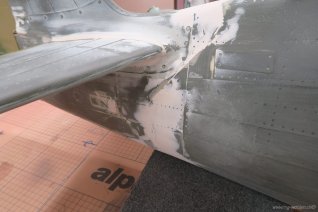
...und dann sieht es so aus
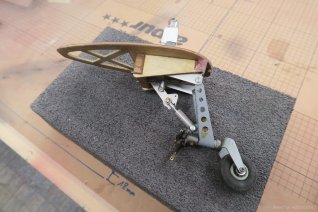
Der Hechradspant vom abgestürzten Modell wird wieder zurecht gemacht
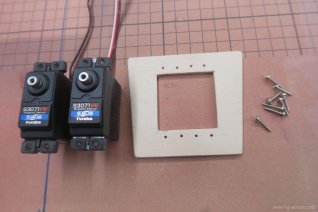
Ein Servobrett für die Höhenruderservos
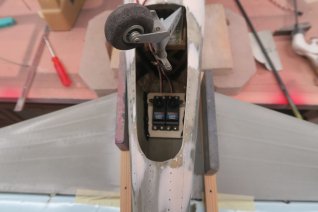
Heckradspant und Servobrett sind eingebaut
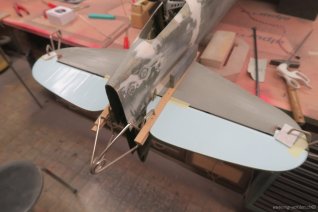
Jetzt werden die Ruder verklebt
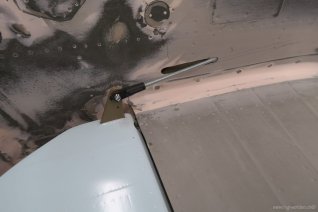
Die fertige Ruderanlenkung
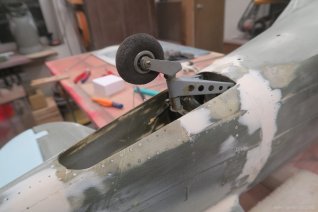
Das fertig eingebaute Heckfahrwerk ist noch nicht angelenkt
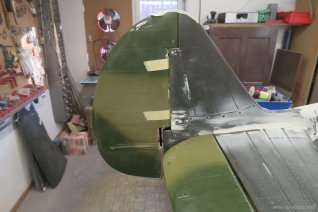
Jetzt wird das Seitenruder angepasst
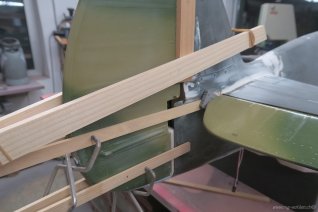
Hier wird der Abschluss Spant fixiert und eingeklebt
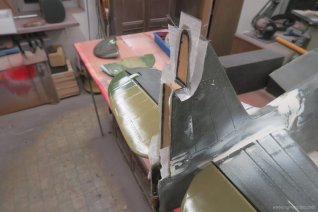
Der Abschluss Spant muss noch mit Glasgewebe verstärkt werden
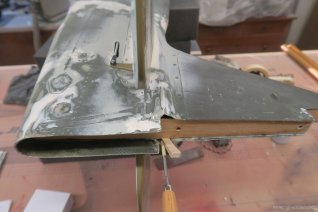
Die Bowdenzug Rohre für die Ruderanlenkung werden fixiert und eingeklebt
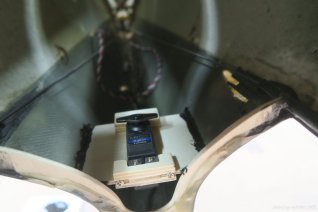
Im Rumpfrücken ist das Seitenruder Servo untergebracht
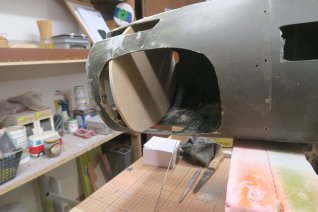
Ein neuer Motor Spant muss angefertigt werden
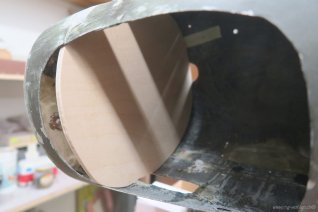
Der Spant muss überall angepasst werden
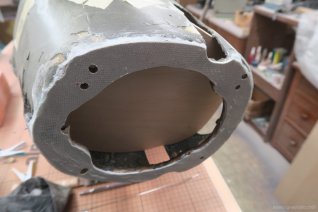
Nach dem einkleben wird der vorderteil abgetrennt
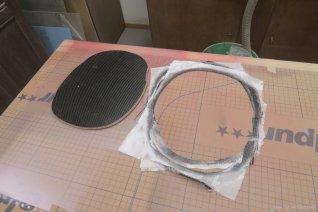
Beidseitig mit zweimal Glas und einmal mit Kohlegewebe laminiert
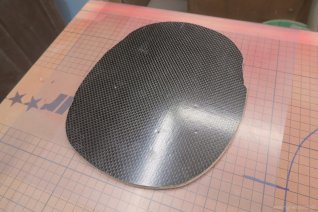
Der fertige Spant
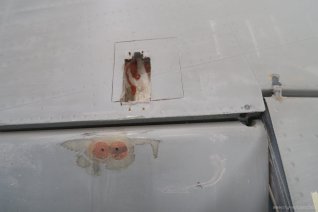
Die Querruderservos werden neu liegend eingebaut

Entfernen vom GFK Laminat
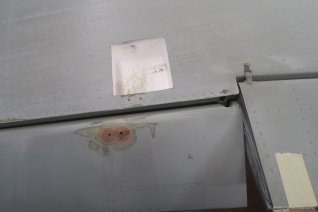
Styropor ausschneiden
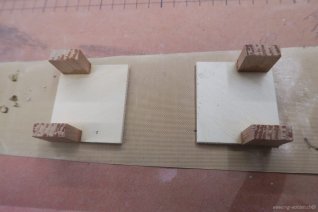
Servohalter vorbereiten
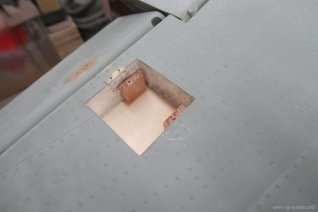
Die Servohalter sind eingebaut

Die Haltelaschen sind mit Doppelklebeband am Servo fixiert
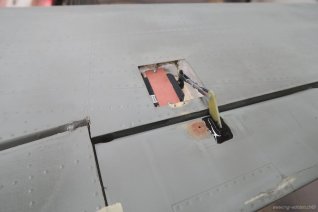
Servo eingebaut und angelenkt
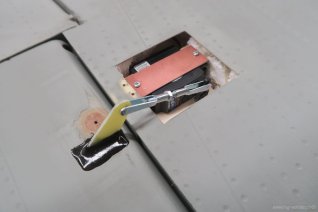
Der Ruderhebel muss bis auf die Oberschicht reichen
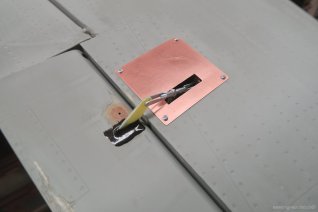
Die Servoabdeckung besteht aus Printmaterial
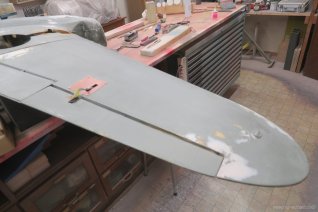
Auch die Querruder sind fertig
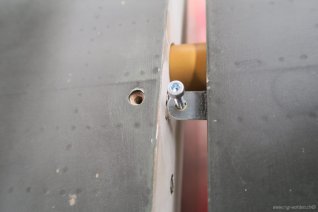
Das ist die Flügelsicherung
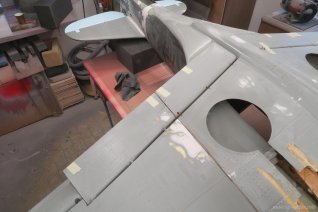
Weiter geht es mit den Landeklappen
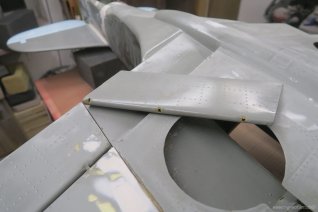
Die alten Scharniere sind ausgefräst
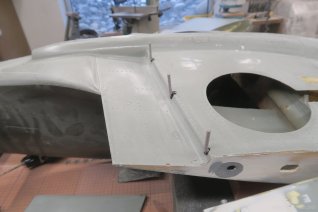
ie Landeklappenscharniere sind gesetzt
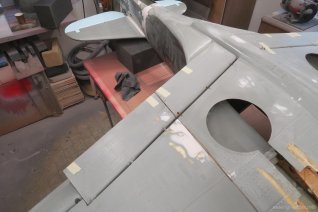
Die Mitnehmerlasche ist eingeklebt
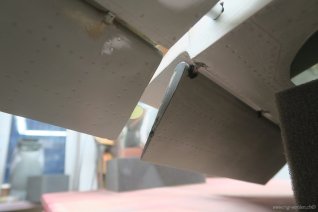
Die Mitnehmerlasche von unten
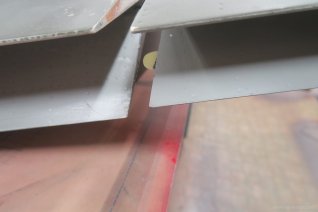
Die Mitnehmerlasche von oben
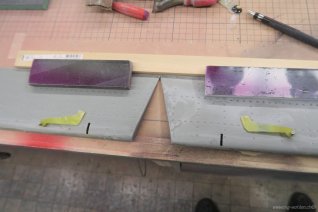
Die Ruderhörner für die landeklappen
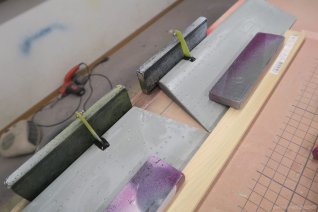
Die Ruderhörner müssen symetrisch eingeklebt werden
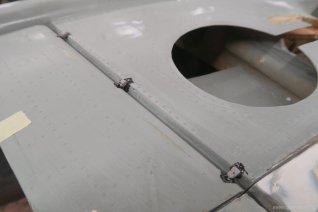
Der Drehpunkt ist nicht ganz ideal
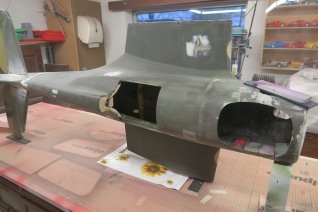
Die Spanten werden noch mit GFK überzogen
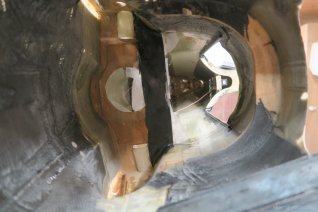
Das alles muss noch verputzt werden
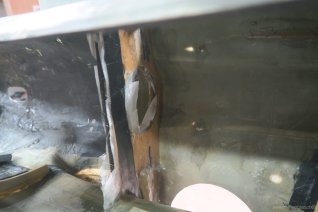
Schlechte Arbeitsverhältnisse
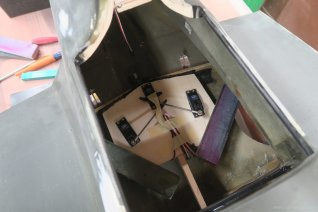
Nach dem Verputzen kann die Servoplatte eingeklebt werden
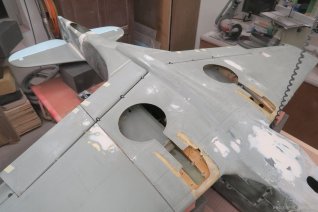
Nochmals zusammenstecken um die Passung zu kontrollieren
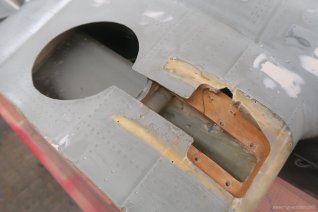
Baustelle Fahrwerk
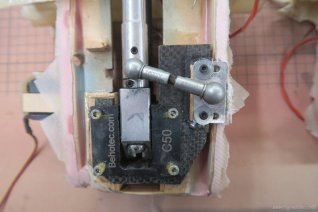
Das alte Fahrwerk wird vermessen und dann ausgebaut
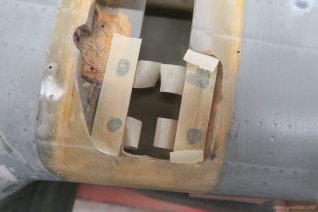
Die alten Löcher sind mit Harz aufgefüllt
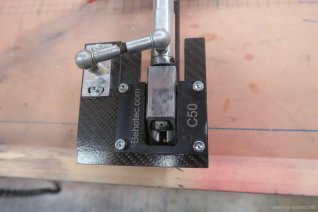
neue CFK Platten werden hergestellt
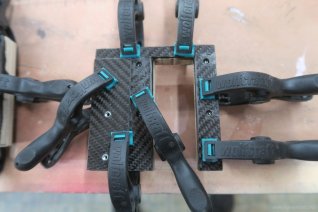
Die Halteplatten werden entsprechend aufgefüttert
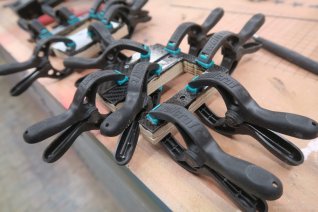
Aushärtezeit
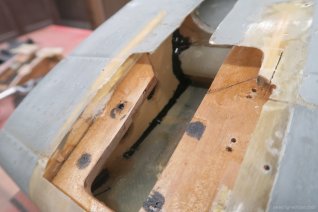
Diverse Stellen so gut wie möglich nachkleben
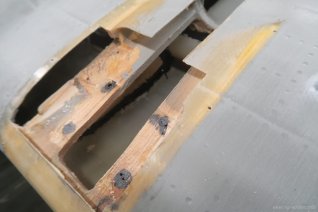
Altes Holz wird entfernt
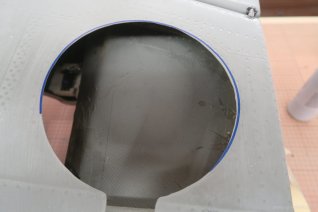
Die Öffnung für das Rad muss noch angepasst werden
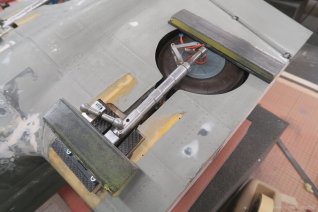
Die ganze vorbereitete Einheit kann jetzt eingeklebt werden
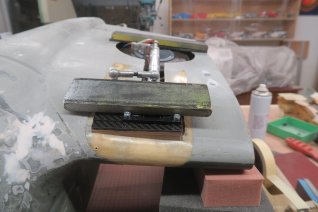
Kontrollblick
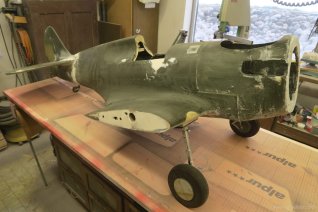
Und jetzt steht er auf den eigenen Beinen
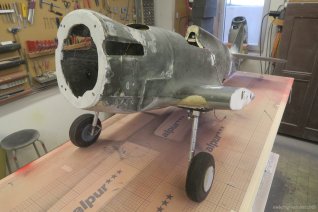
Das Fahrwerk wird zur Kontrolle ein paar mal ein und ausgefahren
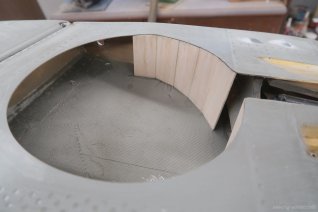
Der Radausschnitt muss noch verkleidet werden
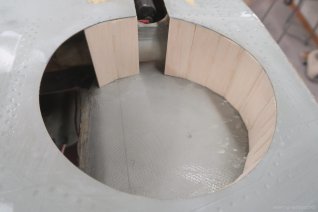
Stück für Stück wird eingesetzt
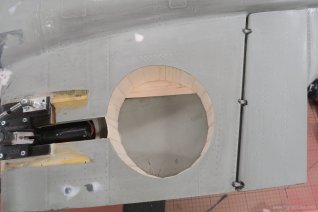
Radkasten fertig zum Glasen
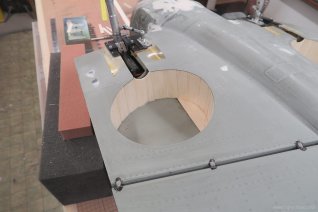
Vorbereiten für die Abdeckung
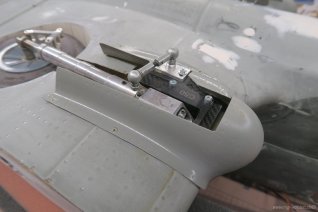
Die Abdeckung mit eingefahrenem Fahrwerk
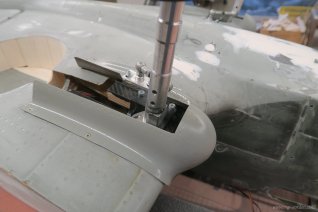
Die Abdeckung mit ausgefahrenem Fahrwerk
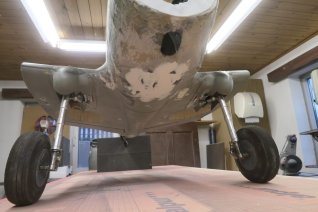
Der Fahrwerkswinkel muss nochmals angepasst werden
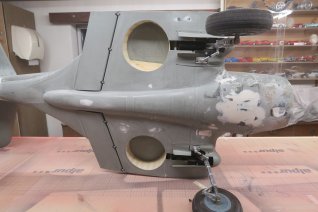
Die ganze Einheit von unten
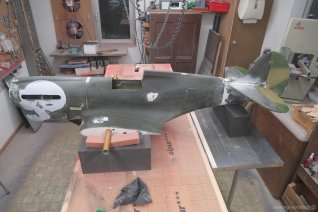
Eine neue Kabinenhaube muss noch angefertigt werden
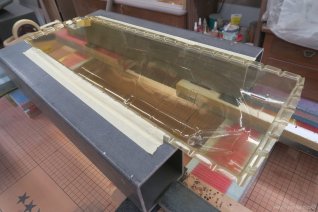
Eine alte Kabinenhaube wird als Negativ benutzt
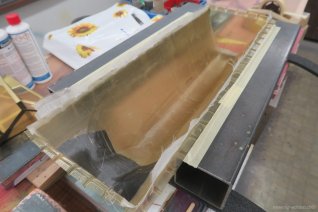
nach dem Trennmittelanstrich ist innen alles mit GFK auslaminiert
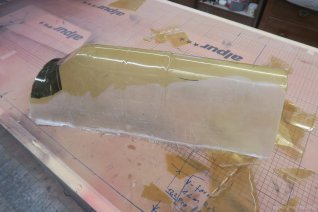
Das Entformen gestaltet sich schwierig
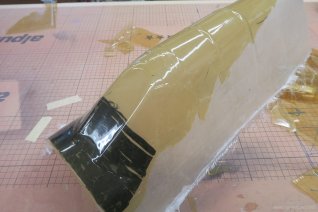
Die alte Haube ist sehr spröde
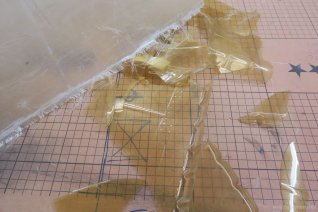
Restmaterial
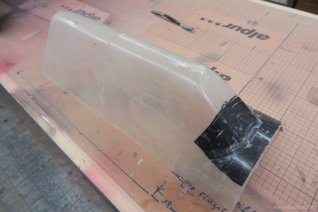
Ausformen geschafft
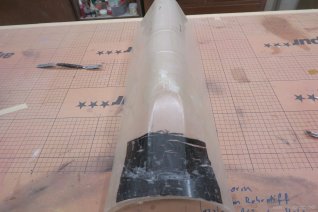
Hier sieht man die Konturen
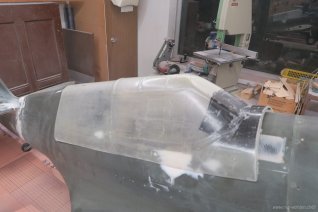
Anprobe
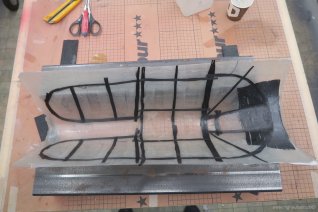
Überall werden noch CFK Rowins eingelegt
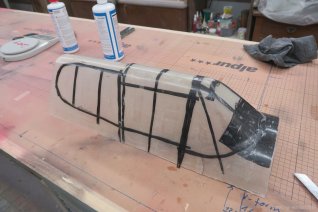
Die Rowings sind nochmal mit 49g GFK überlaminiert
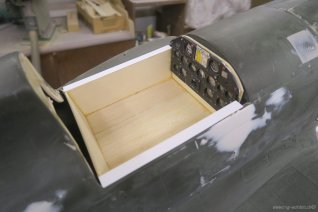
Hier wird die Puppenstube angepasst
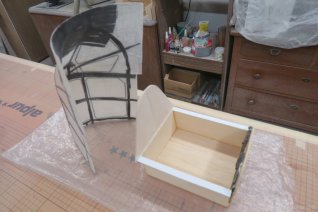
Die Rückwand wird an der Haube angepasst
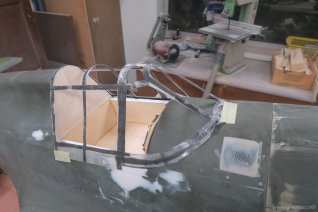
Haubenrahmen fertig ausgeschnitten und angepasst
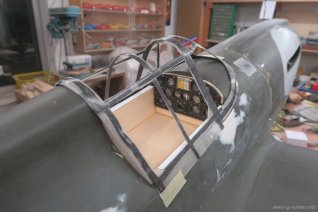
Die Scheiben werden später von Kurti eingepasst
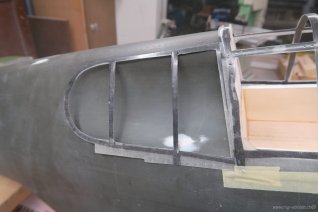
Der hintere Scheibenrahmen
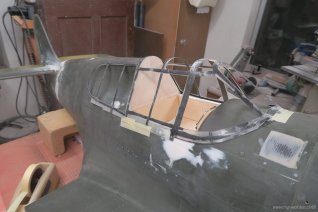
Hier wird die Verschraubung vorbereitet
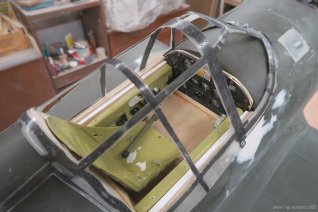
Kabinenhaube fertig für den Finish
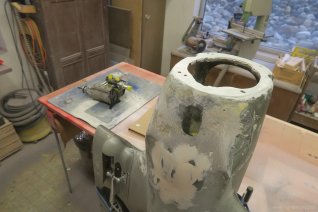
Nun wird der Treibling eingepasst
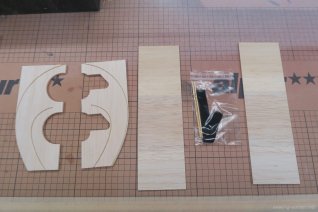
Der Bausatz für die Kühlluftführung
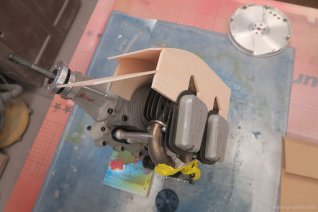
Die Ausfräsungen passen perfekt
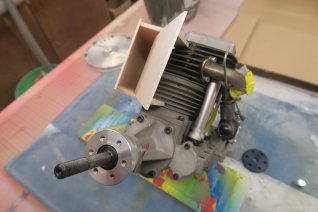
Das überstehende Balsaholz wird entfernt
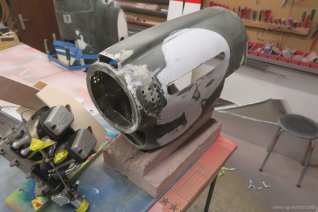
Erstmal schauen wie die ganze Einheit in die Haube passt
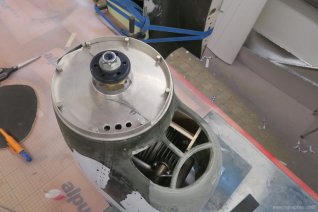
Der Motor wird hängend und leicht Schräg eingebaut...
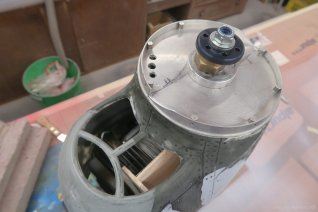
... und so gewinnen wir auf der anderen Seite Platz
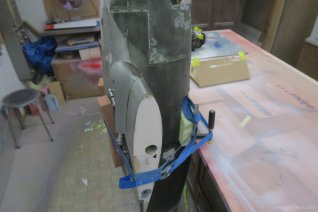
Jetzt muss der Rumpf richtig gut fixiert werden
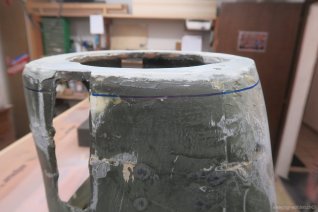
Nach dem Ausmessen wird angezeichnet...
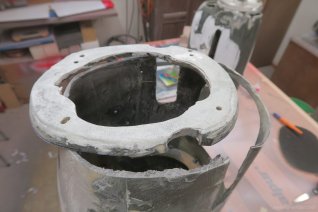
... und gnadenlos abgeschnitten
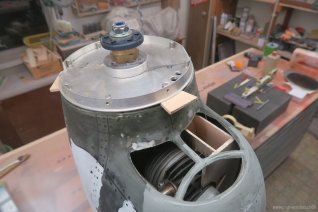
Der Motor wird mit dem richtigen Spaltmass in die Motorhaube gehängt
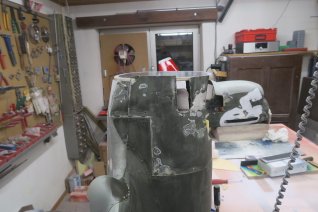
Der Motorspant ist am Rumpf angepasst
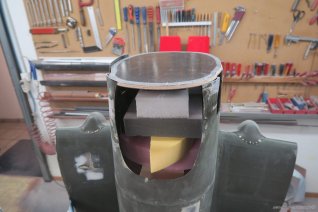
Der Motorspant ist federnd auf Schaumgummi in den Rumpf eingelegt
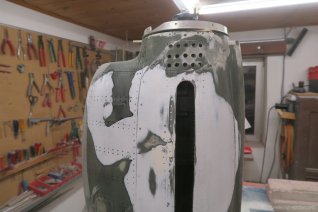
Jetzt kann die Motorhaube mit dem eingehängtem Motor am Rumpf angeschraubt werden
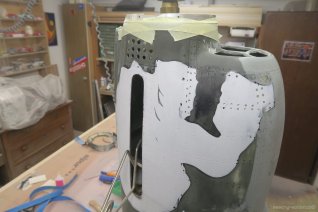
Der Motor ist mit Klebeband fixiert und der Spant zum anheften mit Klammern am Motor gesichert
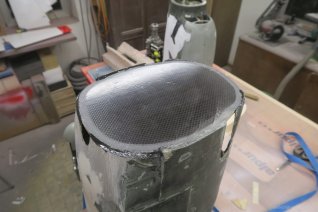
Nach dem entfernen von Haube und Motor
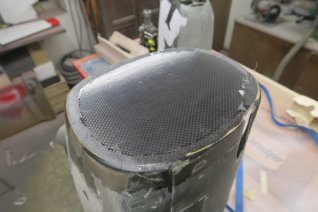
Laminieren mit 49g GFK Gewebe
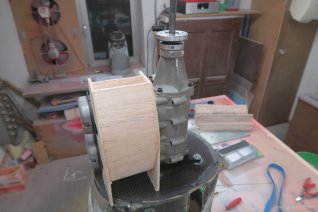
Der Motor ist verschraubt
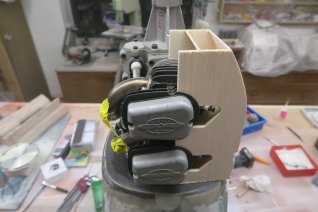
Die Platzverhältnisse sind nicht üppig
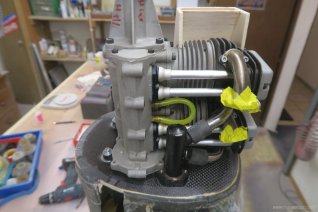
Die Öffnung für den Vergaser muss noch ausgearbeitet werden
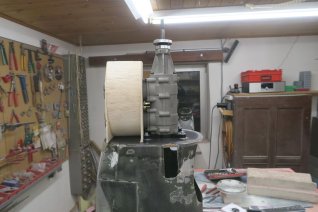
Kontrollblick
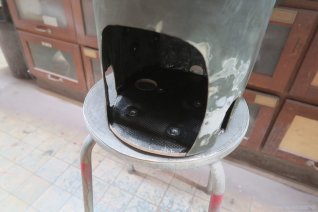
Der Spant wird von innen am Rand noch ausgegossen
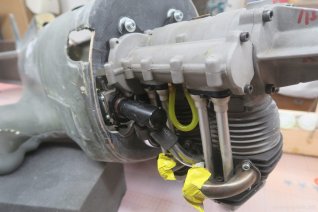
Vergaseröffnung fertig
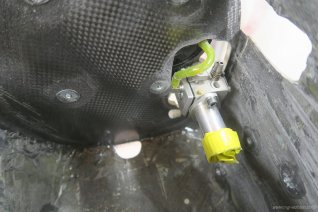
Ansicht von innen
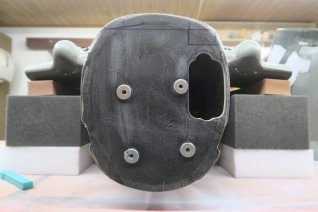
Die Öffnung für den Auspuff ist angezeichnet
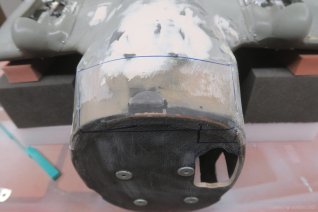
Das alles muss weg
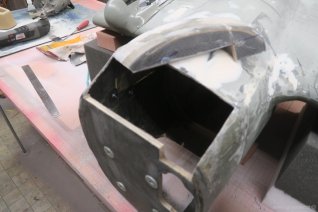
Zuerst wird zu gemacht dann wieder aufgefräst...
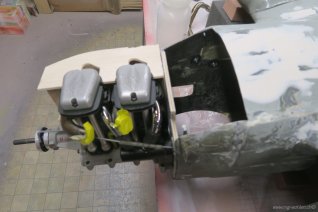
...aber es muss sein
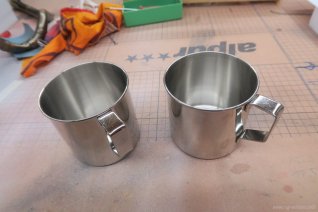
Diese dinger sind nicht für den Kaffee...
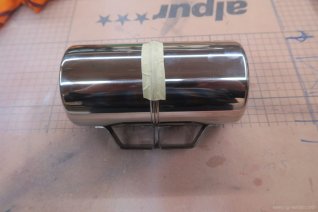
...sondern für den Auspuff
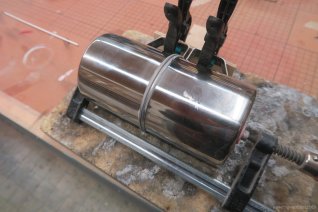
Die Tassen werden stirnseitig zusammengelötet
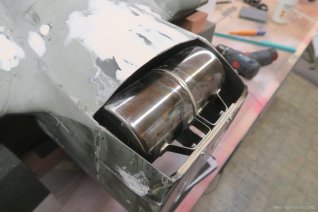
Die Öffnung am Rumpf wird am Auspuff angepasst
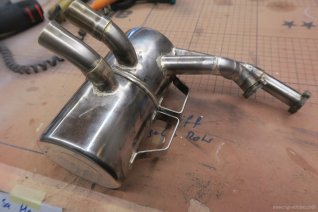
Restrohre wurden verarbeitet
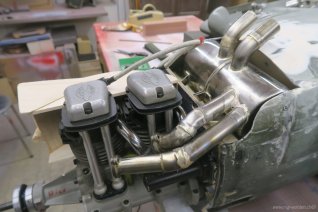
Der montierte Auspuff von unten

Die angepassten Auspuffkrümmer
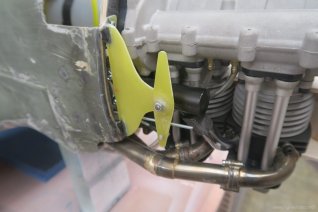
Die Vergaseranlenkung muss umgelenkt werden
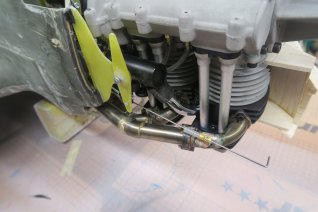
Der Choke wird von Hand betätigt
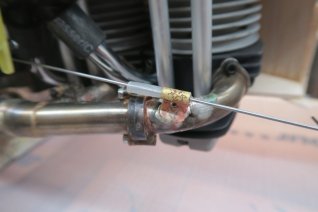
Die Silikonlagerung vom Choke Gestänge
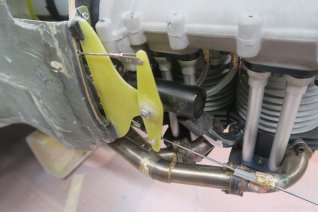
Die komplette Vergaseeranlenkung
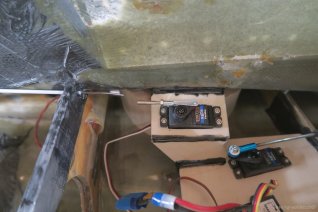
Das Gestänge vom Gasservo wird erst am schluss verlötet
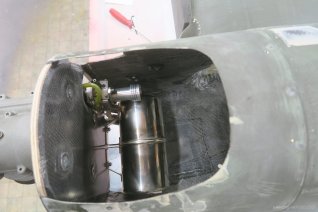
Der Auspuff muss noch verkastet werden
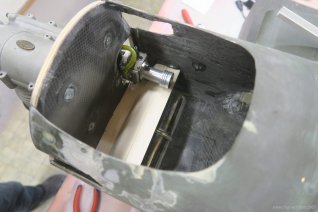
Stück für Stück wird mit Balsaholz verkastet
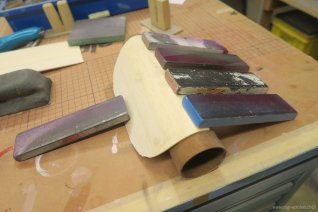
Das hintere Teil wirde vorgebogen
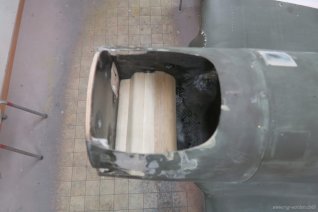
Die fertige Verkastung
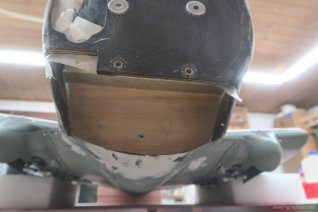
Die ganze Verkastung wird mit Glas überzogen
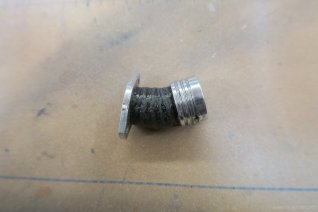
Der Ansaugbogen muss auch angepasst werden
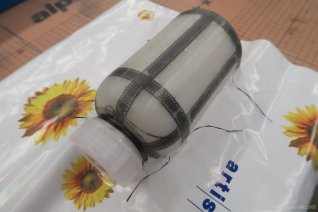
Eine Tankhalterung in GFK und CFK
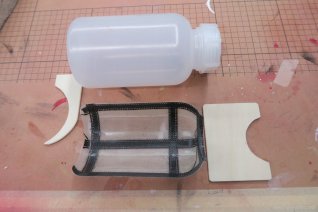
Die Einzelteile der Tankhalterung
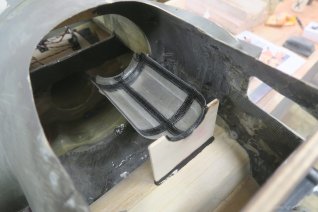
und so wird die Halterung eingeklebt
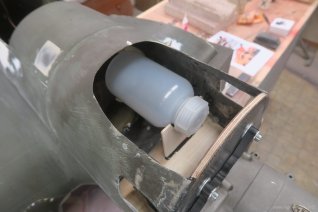
Der Tank passt perfekt
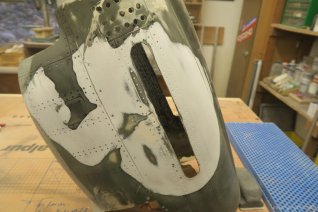
Hier fehlt noch Etwas
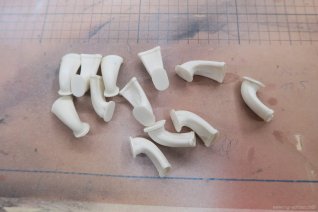
Diese Dinger müssen noch eingeklebt werden
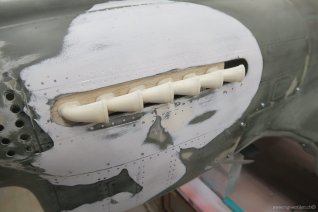
Die Auspuffrohre sind auf ein Hartbalsastreifen aufgeklebt
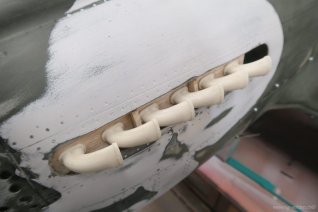
Dies muss noch von innen mit GFK versteift werden
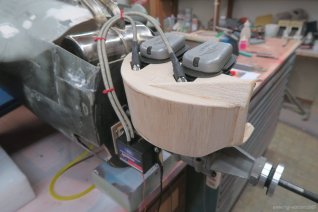
Die Zündung an ihrem Platz
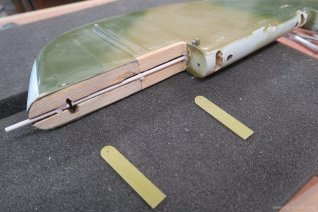
Der Drehpunkt am Seitenruder war an der falschen stelle

Diese GFK Teile sind eingefettet um....
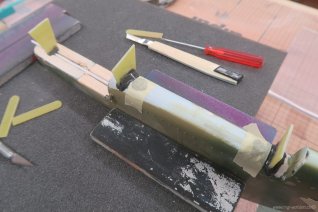
...nach dem ausgiessen wieder heraus zu nehmen
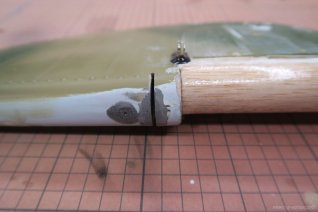
Die Schlitze nach dem verschleifen
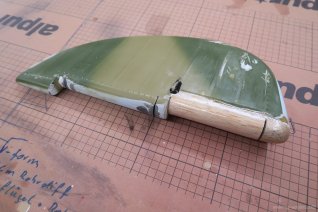
Das fertige Seitenruder
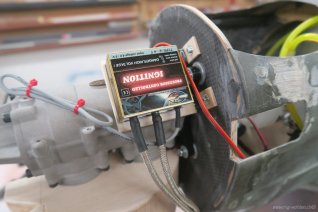
Die neue Zündung hat ein anderes Mass als die alte und muss umplatziert werden
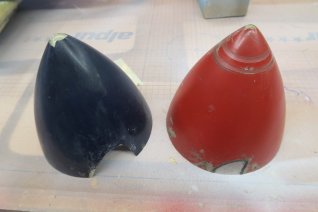
Bei diesen Spinnern werden erstmal alle Löcher verschlossen
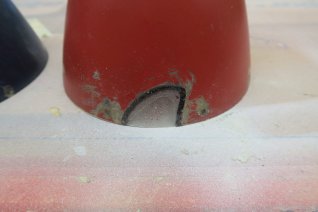
Dies wird noch verspachtelt und dann neu ausgeschnitten
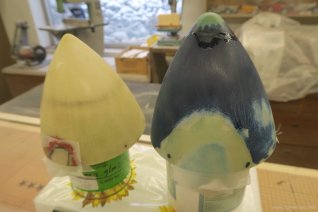
Die verschlossenen Löcher sind bereit zum verschleifen
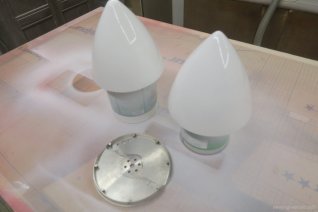
Die Spinner sind gespachtelt und weiss gespritzt
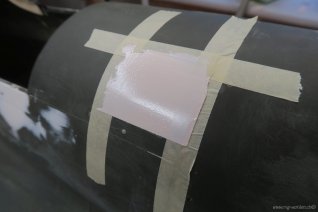
Auf dem Rumpf wird noch ein Deckel aufgespachtelt
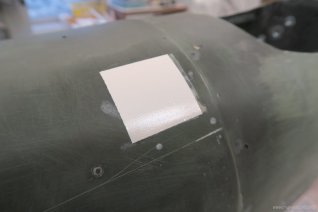
Das Klebeband muss noch im weichen Zustand entfernt werden
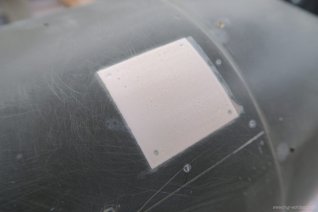
Fertiger Imitations Deckel
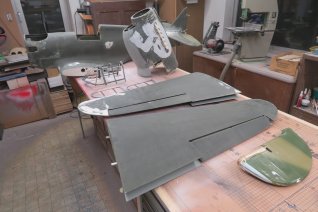
Alles demontiert verschliffen und zum Spritzen bereit
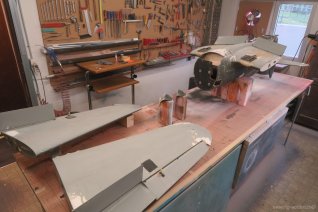
Und los gehts mit der Spritzorgie
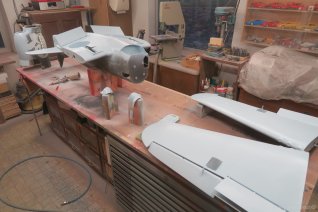
Zuerst die Unterseite in Blaugrau
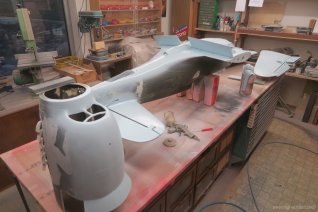
Für die Unterseite wurde nicht viel abgedeckt
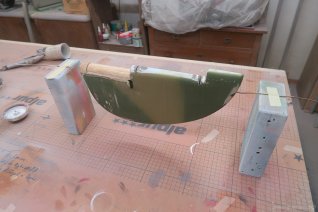
Das Seitenruder wird aufgebockt
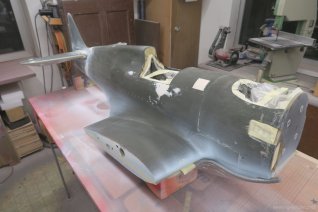
Nun ist die Oberseite am Zug
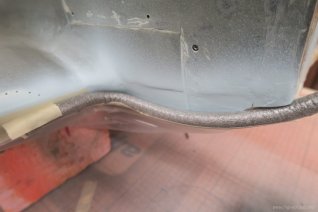
Die Wulst sorgt für eine weiche Kante
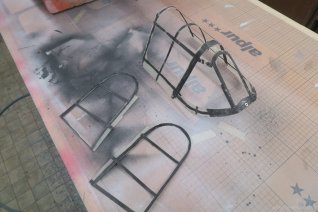
Auch der Haubenrahmen muss gespritzt werden
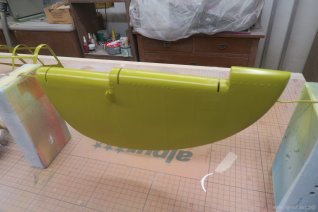
Seitenruder in Grün
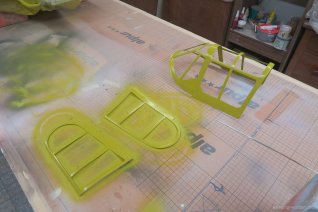
Der Haubenrahmen in Grün
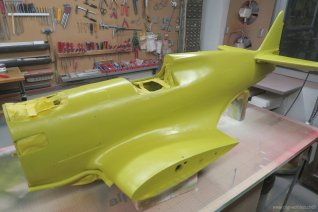
Nach dem Trocknen ist die Grundfarbe seidenmatt
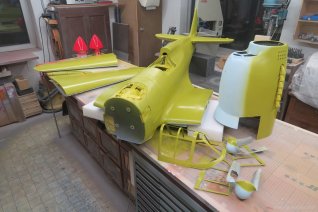
Die Grundfarbe sitzt
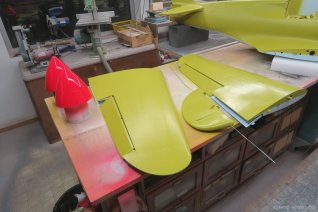
Man bedenke dass auf den Fotos alles viel schöner aussieht
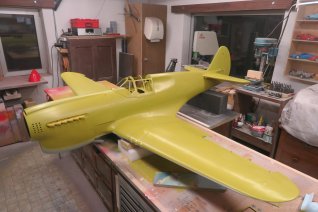
Für die nächste Farbe wird der Flieger zusammen gestellt
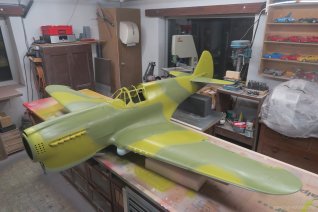
Die letzte Farbe wird freihand aufgspritzt
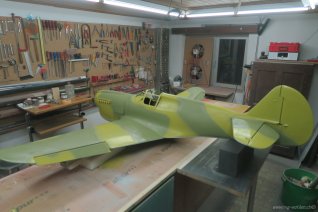
Ich glaube das kann sich sehen lassen
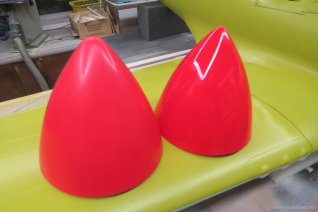
Ein Spinner ist schon mattiert
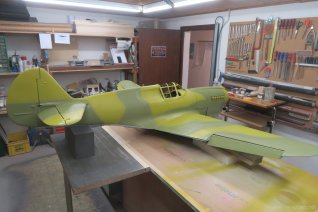
Jetzt gibt es eine Pause und der Flieger geht für die Schiebebilder zu Kurt