
So soll mein neues Projekt in SemiScale aussehen

Der vergrösserte Plan im Massstab 1zu3.5 ist angekommen

Der Roto 125 hat gut Platz

Kontrolle der Fahrwerksmechanik

Die ersten Rippen werden ausgesägt

Das sind die Wurzelrippen bei dem Flügelanschluss am Rumpf

Rippe um Rippe wird mit der Bandsäge ausgesägt

Diese Rippen müssen später noch erleichtert werden

Die Rippen sind zur Kontrolle auf den Plan gestellt

Bis jetzt ist die Passgenauigkeit ok

Meine kleinen Helferlein sind Gold wert

An den Inneren Rippen sind die Öffnungen für die Steckrohre ausgesägt

Der richtige Winkel vom Steckrohr wird festgelegt

Die V-Form ist pro Seite 6 Grad

Es muss genügend Luft für die Steckrohrhülse vorhanden sein

Vorbereitung für den Holm

Stabile Unterlagen sind wichtig

Auch das hintere Steckrohr wird eingepasst

Beide Steckrohre müssen 100 Prozentig paralell eingebaut werden

Die Ersten Erleichterungen sind ausgesägt

Auch die ausnehmungen für die Buchenholme sind gemacht

Zwischendurch musste eingekauft werden

Montage von der Hilfsnasenleiste

Die Endleiste ist ein 4mm CFK Rohr

Der brauchbare Musterflügel

2x3 Stk Styrodurklötze zusammengeklebt

Styrodurklötze verschliffen und Halter eingesetzt

Die Styrodurklötze sind 3x mit 80g Glasgewebe laminiert

Die entformten Radkasten

Der Radkasten wird zur Probe in das Flügelgerippe gelegt

Der Winkel vom Fahrwerk und vom Rad wird festgelegt

Der erste Probeversuch vom Fahrwerksbein ist misslungen

Der zweite Versuch ist schon besser

Der Einbau wird platzmässig knapp

Funktionstest

Jetzt kann der Flügel kopiert werden

Der dritte rechte Flügel in Arbeit

Glück gehabt es sind drei Rechte und drei linke Flügel

Ein Rohbau ist immer schön anzusehen

Ein Zwischenstück als Rumpfteil muss gebaut werden

Alles schön parallel ausrichten

Das Zwischenstück wird fixiert

Jetzt werden die Flügelsteckrohre am Zwischenstück ausgerichtet und verklebt

Es scheint alles gerade zu sein

Nach dem entfernen vom Zwischenstück wird alles gut verharzt

Jetzt kommen Vertsärkungen zum Zug

Jede einzelne Verstärkung muss eingepasst werden

Gut verkleben und pressen

Zum Teil muss gestückelt werden

Die Einschlagmutten sind auch schon gesetzt

Bei den Steckrohren muss die Verkastung zweiteilig ausgeführt werden

Hier sieht man die zweiteilige Verkastung

Für so viele Flügel wird das Platzangebot in meinem Bastelraum knapp

Bis ende Steckrohr ist mit Pappelsperrholz verkastet

Im vorderen Bereich konnte der Holm einteilig verkastet werden

Die ersten Beplankungsbretter sind verklebt

Die Spreizklappen sind im hinteren Teil überlappend

Die entfernung von der Beplankung für das Spreizklappenscharnier

Das Scharnier besteht aus mehreren 4cm langen Bowdenzugröhrchen

Scharnier eingesetzt und Querruder angezeichnet

Seitlich der Klappen muss der Schnitt noch gemacht werden

Am hinteren Rand sieht mann der verklebte Fehlschnitt

Der Schnitt muss auf der oberen Seite vom Flügel sein

So funktioniert die Spreizklappe

Hier sieht man gut die hintere Überlappung

Mit verschiedenfarbigen Bowdenzugrohren ist die Verklebung einfacher

Die seitliche Verkastung bei den Klappen

Jetzt wird der hintere obere Teil auch beplankt

Die Versteifung der Spreizklappen

Einblicke

Ruhepause und überlegen wie es weitergeht

Die Position vom Servo ist gegeben

Eine Probeanlenkung

Funktionsprüfung

Die Anlenkung funktioniert und kann so eingebaut werden

Die Nullstellung im eingefahrenem Zustand

Verstärkungsecken für die Schrauben vom Servodeckel

Bei den Fahrwerkshalterungen wird nochmals eine Verstärkung eingebaut

Später muss das Ganze noch mit GFK überzogen werden

Randbogen vorbreiten

Die Randbogen sind ausgesägt

Die Randbogen Versteifungen sind aus Balsaholz

Randbogen fertig montiert

Die Motage vom Querruder Servobrett

Auch bei den Querrudern dieselben Servoausschnitte in der Beplankung

Die Unterseite kann jetzt beplankt werden

Dieser Teil bleibt offen bis die Fahrwerksbeine geliefert werden

Bei der Nasenleiste muss die Beplankung gut angedrückt werden

Fertig vorbereitet für die untere Restbeplankung

Die Randbogen sind unten auch schon beplankt

Hier braucht es noch ein bisschen Spachtel

Bevor die obere Beplankung aufgebracht wird habe ich alles noch mit GFK verstärkt

Nach dem Aushärten kann verputzt werden

GFK verschliffen und Gewinde freigelegt

Die Scharnierhülsen sind mit GFK überlaminiert

Auch Flügelseitig wird überlaminiert

Das muss alles sauber verschliffen werden

Jetzt geht es an die obere Beplankung

Eine stabile unterstützung ist sehr wichtig

Auch mittig muss der Flügel eine stabile Fixierung haben

Die Unterlage wurde dem Profil angepasst

Der Flügel wird beim Beplanken in die Fixierung gedrückt

Noch schräg anschleifen und der Randbogen kann fertig beplankt werden

Die Flügelgeometrie ist hier gut sichtbar

Da kommt noch eine Balsa Nasenleiste dran

Ein Klebeversuch mit neuem PU Kleber

Die Lüscherbeine sind eingetroffen

Die Hochpräzisen Fahrwerksbeine werden jetzt genau ausgerichtet

Passt perfekt

Jetzt können die Radschächte eingepasst werden

Erstmal das ganze fixieren

Überall ein bisschen übermass

Hier geht es an die Grenze

Die Lage wird bis zum Aushärten mit Keilen gesichert

Jetzt kann beplankt werden

Beim Beplanken wird gestückelt

Die Beplankung um den Radschacht sitzt

Der Holm musste für das Fahrwerkskabel durchbohrt werden

Der Ausschnitt im Radschacht habe ich mit Glas belegt

Ein und Ausfahrtest

Die Querruder sind ausgeschnitten

Zuerst wird seitlich verkastet

Dann wird kontrolliert

Hier kommen noch Scharniertaschen als verstärkung rein

Die Scharniertaschen sind eingeklebt

Zwischendurch werden die Nasenleisten noch angeklebt

Wo gehobelt wird fallen Späne

Hier wird für die Konische Leiste vorbereitet

In das Querruder kommt noch ein Füllklotz für die Anlenkung

Hier wird der Flügel im Querruderbereich verschlossen

Die Dreiecksleisten werden auf die Querruder geklebt

Uups eine Dreiecksleiste ist falsch angeklebt und muss korrigiert werden

Scharniere gesetzt und das Spaltmass ist ok

Ausschlag nach unten

Die selbst gedruckten Servohalter kommen zum zug

Servohalter sind eingeklebt

Das Querruder ist provisorisch angelenkt

Die Servodeckel sind aus hauchdünnem CFK

Vorbereitung der Radabdeckung

Auf die Klarsichtfolie habe ich die Abdeckung gezeichnet

Für eine Funktionsprüfung wird ein Deprondummi ausgeschnitten

Einmal links mit Folie eine Unterlage schaffen

Und auch rechts wird eine Folie aufgelegt

Mit genügend Übermass wird auf der Folie laminiert

Vier Lagen GFK und zwei Lagen CFK werden auflaminiert

Damit das Laminat schön aufliegt wird noch beschwert

Und wieder beschränkt der Platz die Arbeit

Nach dem zurechtschneiden werden die Scharniere positioniert

Die scharniere sind verschraubt

In Richtung Radnabe kommt später noch eine Ausbuchtung hin

Trotz der Rundung funktioniert das Scharnier einwandfrei

Der Schwarze Filzstiftstreifen verhindert das Durchschleifen der Beplankung

Auch die Nasenleisten sind verschliffen

Eine letzte Kontrolle dann werden die Flügel auf die Seite gelegt

Für die Ringspanten habe ich ein Distanzbleistift gemacht

So sollten die Spanten halbwegs die gleich Dicke haben

Das Aussenmass ist vom Plan abgeleitet ent

das innenmass wird mit dem Hitec Werkzeu angezeichnet

Und da kam die Laubsäge zum einsatz

Immer 3 mal dasselbe Spiel

Einige Musterspanten mussten zusammengeschustert werden

Oben rechts sieht man noch die Einzelteile für die Musterspanten

Die wichtigen Spanten wurden noch mit CFK verstärkt

Spanten Erleichterung durch die Laubsäge

Erst mal kontrollieren ob alles passt

Übeltäter Spant Nummer 8 Er ist zu klein

Der neue Spant ist angepasst

So muss es aussehen

Jetzt passt es

Jetzt werden die Spanten ausgerichtet und auf dem Mittelholm verklebt

Die Stringer sind aus 4mm CFK Rohre

Der Rumpfmittelteil ist beim Original nur bespannt

Die spanten für den zweiten und dritten Rumpf sind bereit

Drei noch sehr leichte Rumpfgerüste

Jetzt werden die Rümpfe nummeriert

Um am Rumpf weiter arbeiten zu können müssen Stützen gemacht werden

Der Fahrwerksspant ist vorbereitet

Der Spant ist eingepasst und verklebt

Damit der Abschlussspant im Winkel bleibt wird er beim Verkleben gut fixiert

Ausgerichtet und fixiert

Auch der Motorspant wird im Winkel fixiert

Jetzt wird es schwierig

Der komplette Flügel wird samt den Anschlussrippen in den fixierten Rumpf geschoben

Der Flügel wird ausgerichtet und X mal nachgemessen

Die Anschlussrippen werden vorne am Motorspant fixiert

Auch hinten müssen die Anschlussrippen irgendwie am Rumpf befestigt werden

Verstärkungsringe für die Steckrohrhülsen

Die Steckrohrhülsen sind eingeklebt

Für die Flügelanformung wird eine Papierschablone gemacht

Kontrolle

Mit einer Zwischenlage aus dicker Folie wird Das Balsa auf den Flügel laminiert

Beschweren damit alles schön aufliegt

Die Formgebenden Spanten sind aus 3mm Pappelsperrholz
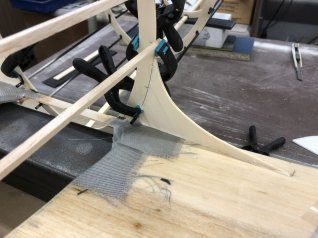
Jetzt können die Spanten angepasst und verklebt werden

Die seiltlichen Spanten müssen einzeln angepasst werden

Der Rumpf ist immer noch labil und muss stabilisiert werden

Alle Rundungen kontrollieren

Hier werden die Flügel wieder montiert um die Rumpfunterseite zu beplanken

Und wieder werden Spanten angepasst und verklebt

Das Füllstück ist aus Styrodur

Zuerst beplanken

Rundung fertig beplankt

Füllstück grob angepasst

Wenn schon denn schon...

Das Füllstück ist in Form gebracht und mit Balsaspachtel verspachtelt

Jetzt geht es mit der oberen Beplankung weiter

Mit Leisten Klammern und Nadeln wird alles fixiert

Langwierige Anpassarbeit Arbeit bei den Rundungen

Eins nach dem anderen

Um Balsaholz zu sparen werden die Bretter in der richtigen Länge zusammengeklebt

Passt
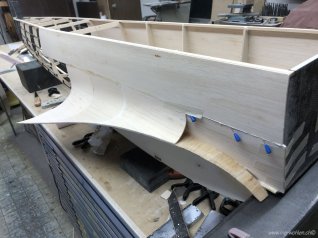
Verschliessen vom Rumpf Vorderteil

Hier muss später noch verstärkt werden

Ansicht von innen

Beplankung am hinteren Flügelabschluss

Auch hier heisst es anpassen und wieder anpassen

Da der Plan nicht stimmt wird nach Fotos gearbeitet

Ein Kompromiss bei den Endleisen wegen Einschieben der Flügel

Die gröbsten Unebenheiten werden mit Balsaspachtel geglättet
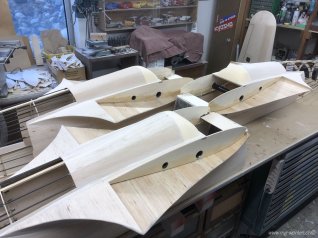
Alle Rümpfe sind an die jeweiligen Flügel angepasst

Die stark gerundeten Beplankungen werden gewässert und vorgebogen

Hier wird eine Abdeckung auf der Beplankung laminiert

Die Motorspant Halterung wird auch nochmals mit GFK nachlaminiert

Im Heckbereich geht es weiter

Für einen Stabilen Stand vom Rumpf muss wieder eine Halterung gemacht werden

Das Seitenleitwerk im Aufbau

Die erste Rippe ist aus Pappelsperrholz

Unterdessen ist auch die Abdeckung ausgehärtet

Jetzt kann zugeschnitten werden

Abdeckung zugeschnitten

Hier wird später die Abdeckung gebraucht

Die Musteranlenkung vom Heckfahrwerk und Seitenruder

Alles scheint zu passen

Hier sieht man die Befestigungen vom Bowdenzug

Alles was passt wird auf die anderen Rümpfe übertragen

Sieht fast aus wie eine Serieproduktion

In diesem Bereich wird auch innen so gut wie möglich nachlaminiert

Ein Kabelkanal für die Höhenruderservos aus Party Trinkhalmen

Jetzt sind auch die restlichen Rippen aus Balsa eingeetzt

Beim beplanken sollten die Flügel montiert sein

Im frisch geklebten Zustand wird das Seitenleitwerk genau ausgerichtet

Für ein verwinungssteifes Rumpfheck sorgt später auch diese Beplankung

Die Kabel für die Höhenruderservos sind eingezogen

Vorbereitung der Höhenruder

Die Rippen sind aus 3mm Balsa

Alle Rippen sind ausgeschnitten

Das Steckungsrohr auf der Suche nach dem richtigen Platz

Das Höhenruder wird auf dem Plan zusammengeklebt

Eine noch filigrane Angelegenheit

Die erste hintere Beplankung am trocknen

Das Steckungsrohr ist noch nicht verklebt

Die obere hintere Beplankung ist auch schon aufgeklebt

Mit der Nasenleiste sind die Dinger schon stabiler
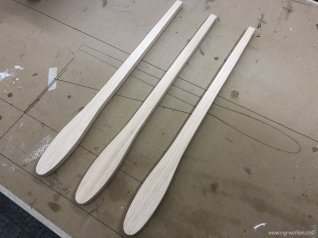
Der Hauptspant für das Seitenruder

Die Rippen werden ausgerichtet

Probesitz

Das Seitenruder wird beidseitig mit 2mm Balsa beplankt

Das Seitenruder passt

Unten muss noch eine Rundung gemacht werden

Auch oben braucht es Vollbalsa zum verschleifen

Das Seitenruder ist anscharniert und verschliffen

Der Rumpfrücken im Aufbau

Ausrichtung der mittleren Formspanten

Vor dem Beplanken braucht es noch eine Fixierleiste

Mit Wasser und allen Mitteln die Rundung erzwingen

Ausrichtung mittels Kreuzlaser

Jetzt kann fertig beplankt werden

Zeit für eine Trocknungspause

Hinterteil fertig beplankt und verschliffen

Die Verdrehsicherung ist montiert

Beim Seitenleitwerk musste der Oberteil abgeändert werden

Der Oberteil muss noch verschliffen werden

Fast fertig

Das untere Loch ist zum einhängen der Anlenkung für das Heckrad und dem Seitenruder

Hier muss noch ein Imitationsblech gemacht werden

So weit so gut

Serienarbeit

Noch können die Rümpfe gut auf den Rücken gelegt wrden

Unterstellböcke für die folgenden Arbeiten an den Rümpfen

So sind die Rümpfe einigermassen standfest

Für die Flügelanformung wird alles abgeklebt

Die erste GFK Auflage ist laminiert

Die Rundung ist mit Microballon verspachtelt und überlaminiert

Im selben Arbeitsgang habe ich gleich den Kabinenhinterteil laminiert

Zur Sicherheit wird noch eine Verstärkung eingebaut

Auch diese Verstärkung wird laminiert

Nach dem Aushärten kann der erste Kabinenspant aufgeklebt werden

Zur weiteren Verarbeitung wird der Kabinenspanst gesichert

Eine Folie als Formgebung und schützt zugleich den Rumpf
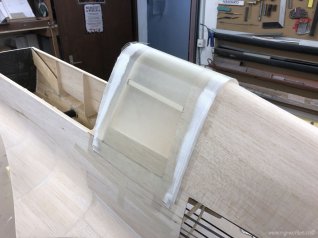
Auf die Folie wird Laminiert mit 3x50g und 2x80g GFK Leinengewebe

Die Musterspanten für den vorderen Rumpfoberteil

Der obere Motorspantteil wird wieder aufgeklebt

Nach langem überlegen wird dieser Teil jetzt fix

Und wieder gewässerte Beplankung aufkleben

Fertig beplankt und verschliffen

Jetzt kann an der Kabinenhaube weiter gearbeitet werden

Der Haubenrahmen ist aus 3mm Pappelsperrholz gemacht

Und wieder beplanken

Der Rumpf muss beim Verkleben der beplankung wieder abgeklebt werden

Auch diese Beplankung ist geschafft

Für die weitere Verarbeitung muss dieses Teil schon laminiert werden

Vorbereitung für das Laminieren vom vorderen Haubenrahmen

Die Folie wird straff über die Spanten gezogen und fixiert

Haubenrahmen fertig laminiert

Hier wird später als Halterung ein überstehender Rand auflaminiert

Das gibt ein Rahmen für die Kugelsichere Frontscheibe

In einer Trocknungsfase werden die inzwischen ausgehärteten Anformungen vom Heckflügel zugeschnitten

Die grob zugeschnittenen Anformungen

Die Anformung für das Seitenleitwerk wird laminiert

Jetzt geht es an die Motorhaube

in Aufsetzspant aus 4mm Pappelsperrholz wird aufgeschraubt

Auf den Spant werden die ersten Styrodurplatten aufgeklebt

Der Seitenriss der Haube

Das muss alles beschnitten und verschliffen werden

Das sieht nach sehr viel Arbeit aus

Mittellinien anzeichnen

Die Länge stimmt schon mal

Nach den ersten Schleiforgien

Es nimmt schon mal Form an

Es ist noch ein weiter Weg

Die Grundform steht

Weitere Anpassungen am Kühler unter dem Rumpf

Anzeichnen der Kühleröffnung

Kühleröffnung angedeutet

Das gibt eine riesenhaube

Zwischendurch mal an der Kabinenhaube weiterarbeiten

Panzerglashalterung angeklebt

Als nächstes wird eine Scheibe eingepasst

Die Scheibe bekommt einen Rahmen aus eingedicktem Harz und Kohlepulver

Nach der ewig dauernden Schleiferei wird das ganze wieder abgeklebt

Das alles muss zweiteilig gemacht werden

Fertig abgeklebt und mit Trennwachs gut eingerieben

Einige Lagen GFK sind am aushärten

Trocknungspause ausnützen und am Höhenleitwerk weiterarbeiten

Bevor das Höhenruder verschlossen wird habe ich den Füllklotz für das Ruderhorn eingeklebt

Die aufgeklebten Leisten müssen noch konisch gesägt und gehobelt werden

Die Ruder sind bereit zum anscharnieren

Ruder anscharniert

Die Randbogen sind angeklebt

Die Verschliffenen Randbogen

Der Servoschacht ist für Servor der 15mm Klasse gemacht

Die Servos sind eingepasst

Diese Servos sollten von der Kraft her reichen

Der erste Kühler ist entformt

Einige Stellen müssen nachlaminiert werden

Eine ausgeformte Motorhaube

Die besäumten Formstücke vom Seitenleitwerk

Diese Teile müssen alle noch nachbearbeitet werden

Nach reiflicher Überlegung werden die zwei Haubenteile wieder zusammengeklebt

Die Trennstelle wird innen und aussen überlaminiert

Die Halterung für einen Drehbaren Rumpf

Die ersten Aufleimer sind mit Klammern und Klebeband fixiert

Anzeichnen der Rundungen

Alles ist verschliffen und bereit zum Glasen

Provisorische Trennlinien

Der Rumpf ist mit 49gramm GFK überzogen

Jetzt kann die Motorhaube zugeschnitten werden

Ein zusätzlicher Spant bringt Stabilität in die Motorhaube

Der Spant ist eingeklebt und die Motorhaube verschraubt

Bei den Schraubenlöchern wird das GFK Laminat nochmals verstärkt

Die Trennlinien für die Lüftungsklappe sind angezeichnet

Die Kühleröffnung ist erstellt

In der Zwischenzeit werden noch Scheiben und Rahmen hergestellt

Der Vorsprung oberhalb der Scheibe muss noch entfernt werden

Ein Fensterrahmen aus CFK verstärktem Harz

Zwischendurch wieder eine Passprobe zur Motivation

Laminieren

Laminieren

Laminieren

Laminieren

Laminieren

Laminieren

Laminieren mit Fremdanteil

Passung nach dem Laminieren immer noch ok

Der Holzdübel mit eingelassenem M3 Messinggewinde

Dübel eingeklebt

Die Verstrebung für das Höhenleitwerk wird vorbereitet

Die Verstrebung muss noch verkleidet werden

Die Halterung ist vergossen der rest muss noch laminiert werden

Die Strebenhalterung am Rumpf und die Seitenruderanlenkung mit Drahtseilen

Ein Verstärkungsspant im Ölkühler

Beim Ölkühlerspant kommt später noch eine Verschraubung hin

Eine Abänderung wegen der Flügelmontage

Nur so kann der Flügel ohne hindernis an den Rumpf geschoben werden

Der abgetrennte Teil ist an den Rumpf geklebt

Das Teil ist mit Glas überzogen und gespachtelt

Das Ende ist abgetrennt und als Klappe in einem anderen Winkel wieder fix angeklebt

Der Spant und die Klappe werden von innen noch mit Glasgewebe verstärkt

Die Flügel unterseite ist mit 50g Leinengewebe überzogen

Bei der Motorhaube werden noch einige Stellen nachlaminiert

Kühlöffnung freigelegt

Die Fensteröffnungen sind angezeichnet
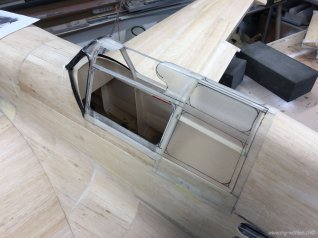
Die ersten ausfräsungen sind gemacht

Dieser Steg im Fenster muss versetzt werden

Blick von vorne

Auch die hinteren Fenster sind freigelegt

Im vorderen Scheibenrahmen sieht man die Verstärkung mittels Kohlerohr

Alle Teile werden jetzt mit einem Schwamm mit verdünntem Spritzspachtel porenfrei eingerieben

Die Motorhaube ist auch mit verdüntem Spritzspachtel eingeschwemmt

Nach einem Schliff mit 120er Schleifpapier ist die Haube mit Spachtel gerollt

Solche Fehlstellen werden mit dem Einreiben sichtbar gemacht und eliminiert

Alle Flügel sind eingerieben

Auch die Kleinteile sind eingerieben

Mein verwendeter Spachtel

Flügel einmal gerollt

So muss es aussehen

So muss es aussehen

Viele Teile in Arbeit

Der Rumpf einmal gerollt

Und es nimmt kein Ende

Alles ist für die zweite Schleiforgie bereit

Und es wird geschliffen

Hier sieht man die Unebenheiten sehr gut

Bei diesem Anblick bekommt man leicht eine Krise

Hier sieht man 4 Stunden Schleifdifferenz

Inzwischen sind 10 Tage intensivschleiferei vergangen

Jetzt können die GFK Formteile verklebt werden

Das Heck ist soweit Rohbaufertig

Die Kabinenhaube ist vorbereitet für die Anpassung der Scheiben

Die Scheiben sind zugeschnitten und markiert

Die Imitation der Haubenschiebe Mechanik

Im hinteren Teil ist noch eine Erhöhung

Unter dem Klebeband ist ein Magnet eingeklebt

Das Magnet hält den Stahldraht in der Position fest

Das ganze fertig verspachtelt

Der Motordom für ein Valach 120 in Vorbereitung

Der Motor wird mit ganz leichtem Rechtszug eingebaut

So ist es leichter den Motor zu positionieren

Der Motor wird ausgerichtet

Nach dem Ausrichten wird der Dom ausgefräst

Auch der Spinner muss sitzen

Das Spaltmass ist ok

Das Spaltmass ist ok

Hier kommt die Kühlluft rein

Der ganze Dom wird gut verklebt und beidseitig laminiert

Vorbereitung für die Auspuffbänke

36 Rohre werden zugeschnitten

Nicht ganz Scale aber für mich ok

Noch ein bisschen gequetscht und dann eingeklebt

So wird die Auspuffbank montiert

Lufthutzen Fertigung

Rohling geglast und gespachtelt

Erster Zuschnitt

Ausschnitt an der Haube mit Schablone

Einpassen der Hutze

Hutze eingeklebt

Die Hutzen werden noch nachgeklebt

Die Ausbuchtungen an den Fahrwerksklappen

Sollte passen

Die Einschlagmuttern für die Flächenhalterung am einkleben

M5 Rändelschrauben

Weiter geht es mit dem ROTO Motoreinbau

Die Schablone für die minimalausfräsung

Die Frontplatte vom Motordom

Der Motordom muss 8cm in der Länge aufbauen

So wird der Motor mit Dom in die richtige Stellung gesetzt

Die Mitte stimmt

Das Spaltmass stimmt auch

Auch die Auspuffrohre haben genug Abstand zur Haube

Jetzt wird angezeichnet

Der Brandspant ist nach dem Mass vom Dom ausgesägt

Der Dom kann angeklebt werden

Zur Kontrolle wird alles wieder montiert

Jetzt kann der Auspuff angepasst werden

Diede Krümmer müssen noch bearbeitet werden

So ist es ok

Passt

Die Verbindungen mit Wellschlauch

Alles hat noch genügend Abstand zum Holz

Alles wieder demontiert um den Dom zu glasen

Um die Unebenheiten besser zu sehen wird alles nocheinmal mit eingefärbten Spritzspachtel gespritzt

Um die Unebenheiten besser zu sehen wird alles nocheinmal mit eingefärbten Spritzspachtel gespritzt (2)

Um die Unebenheiten besser zu sehen wird alles nocheinmal mit eingefärbten Spritzspachtel gespritzt

Der erste Versuch Mit Spachtel die Blechstösse zu imitieren

Der zweite Versuch mit eingedicktem Epoxy

Mit 2K Spachtel gelingen die Stösse am besten

Die Hutzen werden von innen auch noch verklebt

Mit dem richtigen Platz der Hutzen musste ich ein bisschen schummeln

Hier muss noch gespachtelt werden

Die hintere Hutze ist genau auf dem Brandspant

Hier sieht man gut dass der Brandspant in die Quere gekommen ist

Das sind die Löcher für die Oel Einfüllstutzen

Und das werden die Schraubdeckel für die Einfüllstutzen

Einfüllstutzen montiert

Dieser Versuch mit Stahldräte löten ist misslungen

Mit CFK Stäbchen geht es fix

Die kleinen Details beleben das Erscheinungsbild

Die Blechverstärkung ist mit Klebeband gemacht

Blechstösse überall

Kleine vorstehende Nieten sind mit Weissleim gemacht

Dem Spinner wurde die Nase abgesägt und umgedreht wieder eingeklebt

Der verschliffene Spinner

Blechstösse am Seitenleitwerk

Eintrittsluke und Servicedeckel

Die erten Bandscharnier Imitate sind aufgeklebt

Zur Kontrolle werden die Blechstösse überspritzt

Trimmruder am Seitenruder

An den Details kann man sich verweilen

Da und dort noch etwas aufkleben

Aufspachtelung am Heckflügel

Randverstärkung am Höhenruder

Es geht an den Flächen weiter

Detail an den Flächen

Nietapparat

Die ersten Nieten sind gesetzt

Diese Nieten sind ein wenig gross geraten

Nieten an der Motorhaube

Rahmen für Positionslicht

Nieten auf den Rippenverstärkungen

Der ahnt etwas

Ein Sitz muss angepasst werden

Der Sitz wird fixiert

Die Höhe passt

Jetzt noch Cabrio

Die Überrollbügel sind aus Balsarundstäbe

Kontrolle

Das Armaturenbrett fehlt noch

Das Armaturenbrett ist erstmal vorbereitet

Jetzt geht es weiter mit der Motorkühlung

Mit Balsastreifen wird ein Kanal am Motor angepasst

Lufteinlass

Der Kanal wird oben verschlossen

Stück um Stück ankleben und passend abschleifen

So sollte es in Etwa passen

Ob dies so funktioniert wird sich noch zeigen

Die profisorische Halterung

Kontrolle ob die Öffnung passt

Das ganze konstruckt ist sehr leicht

Innen mit Harz ausgestrichen aussen beglast

Und so sieht es fertig aus

In die motorhaube habe ich noch eine Versteifung einlaminiert

Der Rumpfhinterteil ist mit silbriger Gewebefolie verschlossen

Die erste Farbe auf den Flügelunterseiten

Farbe auf der Rumpfunterseite

Farbe auf dem Rumpf

Kabinenrahmen auch gespritzt

Details aber auch die Fehler kommen jetzt zum Vorschein

Und immer wieder abdecken

Innenraum Bemalung

Innenraumbemalung

Minimalistisches Armaturenbrett

Auch das Weiss und Rot ist aufgebracht

Spinnerkappe

Seitenruder

Detail Randbogen

Detail auf dem Flügel

Die Seitenruderanlenkung

Die Servos für das Seitenruder und Heckfahrwerk

Hechfahrwerk und Höhenruderanlenkung fertig

Und das muss jetzt sein

Die vordere Tankhalterung

Tankhalterung fertig und der Tank mit Gummi fixiert

Die Wärmeabschottung beim Auspuff

Die Wärmeabschottung von unten

Die Scheiben werden bis zum Aushärten mit Magneten fixiert

Alle Scheiben sind mit Canopy Glue eingeklebt

Der Pilot ist auch angeschnallt

Jetzt kann der Motor Fix eingebaut werden

Choke anlenkung und Benzinzufuhr sind gemacht

Die Jetzige Schwerpunkt Analyse ohne Flügel ist ok

Querruder Anlenkung fertig

Fahrwerk fertig eingebaut

Die Radabdeckung ist fertig montiert

Servodeckel verschraubt

Landeklappen betriebsbereit

Kühlerimitation eingebaut

Es passt noch alles zusammen

Das Fahrwerk geht am Transportgestell vorbei

Der fertige Fliegerrollator

Rollator inkl. Montage Werkzeug

Wir machen ihn ca 60 Jahre älter

Die Auspuffbank

Und noch mehr Dreck

Abzeichen der Pilotenschule Emmen

Detail Flügel

Detail Randbogen

Rollout 1

Rollout 2

Rollout 3

Rollout 4

Unterdessen ist auch der 28 Zoll SL Propeller eingetroffen

Propeller montiert

Bereit für den nachsten Probelauf

Der Probelauf Mit Sl Propeller